
The fingerprint is a vital step in ensuring repeatable print and maximizing the tonal range output of your press. A press fingerprint documents how your press prints with the variables (inks, tapes, anilox rolls) identified during the press optimizations. It also helps get the press to a known, repeatable state by measuring density and dot gain. Repeatability is key. If you can’t repeat it, don’t waste your time!
Before you fingerprint, you need to optimize your process. Optimization is defined as identifying the best set of variables to achieve your design regimens. This step is commonly skipped in an attempt to save time, but if you don’t optimize you may not achieve your optimal print results.
During the fingerprint, we identify the solid ink densities that the press will achieve with the anilox rolls, inks, tapes, plates and substrate we are using (determined by the optimization). During the fingerprint, measure your densities. These densities should now be carved in stone as your targets. Once the targets are identified, you should be able to repeat them. Simply put, when we use this set of components, you will achieve these densities. It’s really that easy!
It is vitally important that a fingerprint is completed under normal, repeatable conditions. You need to be able to achieve (repeat) the outcomes (densities and dot gains) every time you are on press. It is critical that the anilox rolls are clean, the correct mounting tape is used, and ink is in spec (pH and/or viscosity). Documenting the press setup is useful and a great way to assure repeatability.
Related story: Press Optimization: Setting the Foundation for Quality Print
Many people ask me, “What should my target densities be during my fingerprint?” To which, I would simply ask, “What were your density targets during your optimization?” More often than not, the people who ask this question didn’t optimize and therefore, are not ready for a fingerprint. Frankly, there really is no “right” answer as long as you can always repeat your densities.
FIRST (Flexographic Image Reproduction Specifications and Tolerances) densities are a great starting point to be achieved by most printers. These densities are defined as Yellow = 1.0, Magenta = 1.25, Cyan = 1.35, and Black = 1.50 +/- .05. But if you can do better (achieve higher densities) on a daily basis, more power to you! If you can’t achieve FIRST target densities, it’s OK, as long as you know what you can achieve and repeat that every day.
If you are a large printer, it is best to have the same targets for all of your presses. This will streamline the workflow and make managing your proofs or moving work to different presses much easier. If you run your fingerprint and the densities are not falling in line with previously determined targets, then I would verify the press is set up correctly:
- Is the ink bad?
- Are the new anilox rolls engraved correctly?
- Is the dyne level of the material incorrect?
- Are the plates mounted with the wrong tape?
- Is the impression optimal?
Additionally, I would recommend looking back at the optimization to make sure you selected the correct components. More often than not, this error occurs because the printer did not take the time to properly optimize in the first place.
You may need to work with your anilox roll supplier to adjust the volume of your anilox rolls or your ink supplier to tweak your ink formulation. Please note that the fingerprint is not the time to reinvent your ink formulation or change your anilox roll volumes — this should be done during the optimization.
Whatever you do, don’t run it if it is not correct! You are just wasting your time and money.
The other focal point of a fingerprint is assessing the dot area or the dot gain. It is important to note the plates for the fingerprint should be run “linear” or without a curve applied. If there is a curve applied it will be difficult to determine how we need to adjust for your dot gain. In flexo, we typically want our 50% to print as a 68% to 72%. Intuitively, you would think a 50% should print as a 50%, but that is not the case. We use the Murray-Davies formula to measure dot gain, which includes optical dot gain. In short, the dot is just measuring as 68% and not truly printing as a 68%. However, during the fingerprint, it is more than likely the 50% will not print as a 68% and that is perfectly fine. In fact this is what we want. We will make a correction to the dot gain (using software in pre-press) based on data we collected from the fingerprint. The key thing here is to have good and even impression settings. Make sure you have enough pressure that your solids are printing solid, but not too much causing the dots to squash and create halos.
All the press components can influence the printed dot, so it’s critical to ensure the press is in the ideal operating condition (determined during the optimization). Pre-press is going to depend on this data for accurate plate making and once again, it’s absolutely vital that the target is repeatable.
The image below shows the typical data collected from a press fingerprint. As you can see, we have recorded our densities and dot area. The densities achieved are now our targets. Note that our 50% dot is not printing as a 68%. In fact, the magenta 50% is measuring at an 80%.
Pre-press will use this dot gain data from the fingerprint to make a dot gain compensation curve. When a file is ripped, this curve is invoked and will automatically adjust our dot percentage, so the 50% will print as a 68%–72%. The image below is a screenshot of a prepress tool for making curves, Esko Curve Pilot, and visually identifies what the software is doing. The data above illustrates that during our fingerprint, our 50% dot was measuring an average of 77%, yet our target is 68%. This means that with the current press setup, it is gaining too much and we will lose lots of image detail and have poor color balance. The plate cure will cut the 50% dot back so it will now be plated as a 37% and will print as a 68% right where we want it.
The following mantra needs to be a part of your culture throughout the plant and supported by management: Repeatability is key to this entire process. If we can’t repeat our print results, all of the work prepress is doing goes right down the drain. If the operator decides to use a different mounting tape or a dirty anilox roll, the densities and dot gains won't match and neither will the print.
Good housekeeping and documentation are a critical part of this process. Any time you change a major print variable (new ink supplier, new plate supplier) you need to fingerprint your process. It is also common practice to run your fingerprint on your most common materials, for instance: uncoated, semi-gloss, BOPP, and clear BOPP with white ink. All four of these will achieve different densities and may have different dot gains, requiring individual targets and curves.
The information from this fingerprint is the foundation for your print moving forward. If the print does not match the proof, the first thing I ask the operator is, “What are your densities and dot gains?” More often than not, the numbers do not match the targets because the press is not set up correctly. Displaying the targeted densities and dot gains in the run targets is a phenomenal quality control tool. The image below is a great example of this. I know it can be hard to find space, but it is a great tool for communicating the target densities and dot gains to the operators.
In short, the press fingerprint lets us see how the press is printing and allows us to establish a known and repeatable state for us to aim at every time by measuring densities and dot gain. The data collected is the foundation for accurate color on all of the jobs printed on this press. Repeatability is critical for us to achieve a press sample that meets customer expectations. If you can’t repeat your densities or dot gains from here on out, you will have issues with your proofs matching your press.
- Categories:
- Flexographic Printing - Narrow Web

Shawn Oetjen is the flexo trainer at Flexographic Tech in Minneapolis, where he oversees the unique cooperative training program founded by AWT Labels & Packaging and Computype. He graduated from Clemson University with a B.S. in Graphic Communications and also holds two associate’s degrees; one in graphics and packaging and another in computer networking, both from Dunwoody College of Technology. Oetjen possess a wealth of knowledge and experience from working in various capacities within the flexographic industry including education, production, technical service and sales. He has a keen knowledge and understanding of the flexographic process from start to finish. Oetjen is actively involved with the Flexographic Technical Association and received the FTA’s president’s award in 2010. Shawn Oetjen is on the Executive Committee for the Flexographic Quality Consortium and is the president of the Twin Cities Flexo Association.
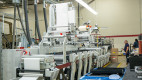




