
Recently, I was at a 3M symposium in Minneapolis when it was made abundantly clear there is confusion regarding target densities for the flexographic industry. In fact, the confusion caused by density specifications is so intense that they were almost removed altogether from the upcoming Flexographic Reproduction Specifications and Tolerances (FIRST) 6.0.
Let’s try to clear up the confusion…
The entire purpose of measuring densities is to identify how much ink you are laying down on your material. Your target densities are what you aim to achieve on your press every day. If you are struggling to achieve your densities, perhaps your targets are not accurate. As a solution, you might require different density targets for different ink systems or pieces of equipment (new vs. old, narrow vs. wide) and that is OK.
I challenge you to go out to your press room and ask your operators what your target densities are. If they know them, great! If they don’t, then you’ve identified a great starting point for improving the process. Process improvement is a critical step in the FIRST process workflow as we all strive to improve our capabilities. Knowing your target densities is an important step in this process. Simply run a fingerprint to benchmark your equipment performance and then use the densities you achieve as your new targets.
FIRST has identified the following density specifications — with the keyword being specifications. These are NOT standards. Many companies have decided to make these their targets/standards without optimizing or fingerprinting their process. Thus there is no assurance that they can actually achieve them every time they are on press.
- Y= 1.0
- M= 1.25
- C = 1.35
- K =1
At Flexographic Tech, my densities are:
- Y= 1.02
- M=1.10
- C=1.28
- K=1.60
As you can see, my densities are NOT the same as FIRST specifications and that is completely OK. What is most important is that I can achieve these densities every single day I go on press. I don’t have to tweak the inks or change the anilox rolls. I simply run the sample up and I am good to go. Density alone is not the only contributing factor for color matching across platforms. Process control or repeatability of the print performance is the most vital aspect of color management.
It’s important to note that great color can still be achieved even if your densities are lower than those specified in the FIRST book. I might even argue that better color separations can be provided if you have consistently low densities rather than random high densities.
I encourage you to run the numbers that make sense to you. If you have been successfully achieving FIRST densities and have great print quality, keep doing what you are doing! However, I am willing to bet that you optimized your process to achieve these targets. At the end of the day, your target densities are what you can achieve every day on press … they do not need to be the same as FIRST.

Shawn Oetjen is the flexo trainer at Flexographic Tech in Minneapolis, where he oversees the unique cooperative training program founded by AWT Labels & Packaging and Computype. He graduated from Clemson University with a B.S. in Graphic Communications and also holds two associate’s degrees; one in graphics and packaging and another in computer networking, both from Dunwoody College of Technology. Oetjen possess a wealth of knowledge and experience from working in various capacities within the flexographic industry including education, production, technical service and sales. He has a keen knowledge and understanding of the flexographic process from start to finish. Oetjen is actively involved with the Flexographic Technical Association and received the FTA’s president’s award in 2010. Shawn Oetjen is on the Executive Committee for the Flexographic Quality Consortium and is the president of the Twin Cities Flexo Association.
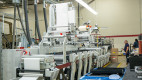




