Zooming Toward Quality
Sophistication across all levels of web inspection technology make it a manageable investment for package printers.
By Susan Friedman
Why buy a Mercedes when you can reliably, stylishly get from Point A to Point B in a Honda? The infusion of sophistication across all levels of web inspection technology makes this analogy ring true for many package printers' purchasing decisions.
"The largest base for video web inspection technology will continue to be simple, inexpensive video systems for general web viewing, while new image-based technology is being developed to bring value-added features to more sophisticated web printing processes," observes Paul Burrows, product application engineer at CC1, Manchester, NH.
Package printers serving the pharmaceutical, security and other industries with stringent packaging compliances and liabilities are common investors in the "Mercedes" of web inspection equipment—those systems employing automated defect detection and 100 percent inspection. Other printers may never need this level of scrutiny. Eddie Engledow, product manager, guiding and inspection systems at Fife, Oklahoma City, says for line work applications, a features-intensive inspection system may just confuse the issue.
On the other hand, a purchase that is too far down the low-end side of the technology spectrum will also muddle inspection objectives. "With video systems, quality counts," states Mike Griese, sales manager, Eltromat Electronics, Chesapeake, VA. "Low-cost, standard web viewing systems will not be able to produce a clear image of the web. Printers will not use the system. Defects will pass undetected."
John Thome, global marketing manager, BST Pro Mark, Elmhurst, IL, estimates that about 10 percent of the market owns a semi-automatic or automatic inspection system, with automation most in demand for registration, barcoding and color monitoring. He believes everyone will go the way of automation in five years, "even narrow-web label applications."
Detective work
It doesn't take an unlimited inspection budget to implement upgraded defect detection capabilities. "All video web inspection systems have benefited from advances in computer processing and display monitor technologies," says Burrows. "Improved, high-resolution, flicker-free display monitors are now standard on all but the most inexpensive systems."
Operators can also maximize defect detection with more precise settings. Engledow recommends making sure tolerances are set high enough to avoid false or inaccurate detection. "Some systems can detect defects as small as 1 mil, but it isn't necessary," he states. "There will always be defects. Printers just have to decide what's acceptable."
In addition, newer software can help prevent false defect alerts by overlooking changes caused by normal system operation, such as video image variance, he says.
Package printers should avoid cutting budget corners by forcing a narrow-web system onto a wide-web press. Thome has seen this attempted in the field as a reality of limited budgets, but warns that narrow-web systems' 2à to 3à field of view could be too small, and traverse speeds, sometimes 1à to 4à per second, may be too slow. "Wide-web inspection fares better with 7à to 9à fields of view, and systems should traverse at least 8à per second," he advises. Many systems, including BST's Eagle, traverse a meter per second.
According to Engledow, Fife's narrow- and wide-web systems both offer the same range of traverse speeds and fields of view for flexibility, but one setting will not fit all. He cautions that a wider field of view won't provide the resolution to view fine print or dot structure of process work.
Another reason to seek out a system that matches a press's parameters is the definitive split between narrow- and wide-web inspection priorities. Jim Doerr, vice president sales and marketing at TruColor Video Systems, LaGrange, GA, says narrow-web applications emphasize cost-effectiveness and general print defects such as misregister, starving ink and hickeys. A lower-end system with manual camera positioning, iris-focus-zoom for magnification, automatic scanning in the web direction, and a compact 12à x 4à camera housing is a common solution, he says.
"There is more emphasis on high-end capabilities in wide-web, particularly for bar code monitoring," Doerr comments. "Because they are running at faster speeds, these printers don't want to stop as often for checks. They are more interested in logging information, and want faster traverse speeds to see more of the web." Popular high-end features include auto-cam positioning, image storage for color matching, and split screen for checking dot gain.
Another high-end trend Doerr cites is Windows-based inspection units designed with open architecture to enable integration with other Windows-based press controls.
"The final decision for a web viewing or web inspection system should be made on image quality and ease of operation," sums up Griese. "This will apply to all markets—narrow-, mid- or wide-web, and line or process work."
Defining automation
An automatic web inspection system does represent a hefty leap ahead in terms of speed and accuracy, but this technology won't eliminate operator set-up or decision-making, and it can't (yet) correct defects.
Griese defines automatic web inspection as a system that inspects an entire run by comparing a live image to a master or reference, and automatically alerts the operator to defects. He contends that consistency will drive automation's adoption. "Printers are being asked to produce not necessarily better quality, but more consistent product, especially for pharmaceutical and security applications. Mistakes can turn into a costly legal issue," he notes, adding that printers can't afford to depend on manual inspection for label features such as foreign languages and patented logos. Hardware cost decreases are making automatic inspection systems' price tags more attractive, he says.
Engledow provides a reality check on automatic system operation. "Operators will always have a five to 15 minute manual set-up time, even with automated systems," he explains. "Programming beyond defect detection, for color monitoring or barcodes, will add minutes to the task." In addition, he notes automated systems typically still require human decision-making. "Operators must determine from the image whether, for example, register is far enough out to make a correction."
Sometime soon, however, more performance responsibility will shift to high-end systems. According to Engledow, suppliers are "working on technology issues" related to closed-loop capabilities—automatic flagging or marking of registration or barcode problems. "I haven't heard a lot of real good success stories yet," he adds.
"Though some systems can stop the press or make a splice when a defect occurs, closed-loop systems aren't at the level where another component can be activated to correct the defect," elaborates Griese. "Many printers are currently opting for integrating a camera with a less expensive off-the-shelf PC, but dedicated hardware and software are needed to fulfill closed-loop."
Karen Huber, director, global sales at PC Industries, Glenview, IL, defines this next level as 100 percent inspection, a contrasting concept to 100 percent monitoring, in which the camera can monitor the entire web via different functions.
"Most printers today cannot justify the costs of 100 percent inspection, but that doesn't mean they don't want it or need it," she claims. "Suppliers must find more economical ways of achieving this technology. In the meantime, video inspection or 100 percent web monitoring can easily do the job for most printers," Huber says, with the exception of pharmaceutical label printers under continuous FDA pressure to improve inspection processes.
"The technology exists for 100 percent inspection, but implementation does not create a return on investment," contends Thome. "The systems that are necessary can cost $500,000." He instead favors defect prevention systems. Instead of flagging defects after they have created waste on-press, defect prevention systems lock in acceptable quality levels of color and other variables, and then alert the operator when the variable is approaching set limits in order to minimize waste.
BAR CODE VERIFICATION EQUIPMENT
Scan-tastic Technologies
Bob Edwards, product manager for Label Vision Systems, says the evolutionary wheel has turned quickly in the past few years for vision-based bar code verification systems, or those that grab a frame of data from the camera for ANSI bar code verification. Edwards sees the next generation in vision-based systems as real-time video decoding, manifested in Label Vision's new Integra 9000 bar code verification system, which processes bar code data in real time without a frame-grabbing system.
A frame-grabbing system can examine approximately two bar codes per second, while a real-time system can examine 60 bar codes per second (per camera), in either picket fence or ladder orientation.
Edwards claims that video-based verification supercedes laser scanning systems in speed and thoroughness, by scanning the entire height of a bar code in .006à increments, or 167 scans for a 1à bar code, regardless of web speed or orientation. The system determines a score for each scan and combines individual scores for a symbol grade.
A laser scanner typically provides scans .01à wide, and can only perform five scans, or .05à of a 1à bar code, at a web speed of 500 fpm, he explains. ANSI guidelines recommend a minimum of 10 equally spaced scans per bar code.
Package printers can expect next-generation, automatic bar code monitoring systems to grade all nine ANSI attributes, at speeds of 100 bar codes per minute, reports Eddie Engledow, product manager, Fife. Here, Engledow cites a sampling of automatic scans these systems provide, along with the defects that will earn a failing grade in each scan.
Edge determination: Excessive bar growth (ink spread) or the presence of large defects.
Minimum reflectance: Bars should be printed darker, or in a color that appears darker under red light.
Symbol contrast: Bars are too light, background is too dark, or both.
Modulation: Ink spread reduces width and intensity of the single module spaces within a bar code symbol.
Voids: Light areas within the bars.
Spots: Dark areas in the spaces.
Decodability: Symbol is incorrectly encoded, or one profile fails to decode due to a localized blemish.
Quiet Zone: Printing in the Quiet Zone, overwrap affecting the restricted area, or symbol is printed too close to substrate edge.





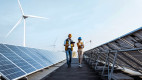