Static Control
Static control and web cleaning are tied together at the hip in the package-printing arena. Moving webs and sheets generate static, and static attracts dirt and other unwanted vermin. So, to consistently supply high-quality product, package printers must pay close attention to the static/contamination Medusa twins.
This area also warrants additional attention due to a couple of hot topics in the world of package printing—the increasing use of film substrates and the coming of static-sensitive RFID electronics. Plastic films generate and hold static charges a lot better than paper substrates (more snakes in Medusa’s ‘do) and the relatively expensive electronic components in RFID tags can get fried by static discharges.
So, although static control and web cleaning have always been a concern, there’s every reason to believe that they will be in the spotlight for the foreseeable future. packagePRINTING talked to some executives in this field of endeavor to get their take on the opportunities and risks in this industry.
pP: What markets (narrow-press, wide-press, offpress) do you target with your product lines?
Mark A. Gibis, vice president of sales, Doyle Systems—We target the printing and converting market. In the printing market, the greatest need for web cleaning/static control would be in packaging (cartons), labels, and corrugated.
Matthew Fyffe, general manager, Meech Static Eliminators, USA—While Meech services all these markets, we tend to concentrate more on the wide-format web converters. Their static-related problems tend to be more severe than those with narrower webs. We also have a very high concentration of product used at the winding stages of these converting lines.
Jay Perry, marketing manager, SIMCO Industrial Static Control—All of the print industry variations (flexo, gravure, web and sheet off-set, as examples) have requirements for static control and/or web/sheet cleaning. Static electricity is often responsible for print and contamination problems.
Jim Patterson, president, Static Clean International—We supply all label printers and screen printers, in-line and off-press. Unit sizes that can be supplied range from 3˝ to 114˝.
Joe Overman, president, TAKK Industries Inc.—Over the years, our product line has consisted of an array of both powered and passive static eliminators and contamination removal products have always had broad application usage. Our product mix is well suited for narrow-press, wide-press, and off-press applications.
pP: Which of these markets do you see having the most need/interest for static control/web cleaning equipment?
Gibis—We find the greatest need exists in the labels, cartons, and packaging.
Fyffe—Virtually all web converters have some need for static control or web cleaning equipment. However, there seems to be a more willingness to invest in static control equipment by those who do printing or packaging in the medical related industries, where dust contamination is a much more costly problem.
Perry—There is certainly significant interest in the flexographic, narrow-press industry (label printing) with all of the excitement generated by the potential that RFID applications offer. The low susceptibility levels that the electronic circuits have to electrostatic discharge (ESD) make this an important market for static control. Quality demands placed on flexo printers today have also increased the need for web cleaners as well, as printers struggle to balance productivity and profitability. The prospect of printed electronic circuits for RFID applications would have a similar impact on wide-web and sheet print applications.
Patterson—Any market where the producer is looking to improve process yields and the finished product quality. Reducing scrap saves on the material being produced, the ink being used, and limits the need for re-runs thus helping to maximize profitability and efficiencies. UV flexo printing applications show the biggest interest.
Overman—We are seeing the strongest need/interest for static controls coming from the narrow- and wide-press markets. As processing speeds and process complexity continue to increase while utilizing more synthetic materials, the need for static controls and web cleaning will continue to be a necessary component of the manufacturing process to maintain higher processing speeds, product quality, operator safety, and comfort.
pP: How important are OEMs in your business model, or do you focus more on retrofits of existing installations?
Gibis—We place high importance on our OEM relationships, but also pride ourselves on our ability to work on a direct basis with custom-engineered solutions for our end users. We do this both on new installations and retrofitting to older existing installations. Doyle’s custom-engineered solutions are based on our more than 88 years of manufacturing experience.
Fyffe—Historically speaking, Meech has primarily focused on the retrofit of existing installations. The problem that an end user sees will vary greatly from company to company, so a “cookie-cutter” static control solution by the OEM will not always address the specific problem that the end user may encounter. With Meech’s broad application knowledge, we are much better able to recommend the correct solution to the specific problem.
However, OEM relationships are becoming a larger and larger part of our complete business model. We have had very good success of late with actually designing and supplying custom equipment unique for that particular OEM.
Perry—OEM relationships are always important to equipment manufacturers. For the print-specific industries, which have traditionally had trouble with static control and web/sheet cleaning, the products and relationships generally evolve as technologies change. Instances like RFID, that happen quickly, usually involve OEM and retail (retrofits as you describe) efforts to help customers solve static problems that impact their production.
Patterson—For the industry to get maximum benefit of our equipment it is essential to build OEM relationships ensuring any supplied production line/press is already set up (at a small extra cost) to enable the end-user to maximize their return in investment. Through this approach, the production line can be set up once and there would be no need for future installation works and breaks in production.
Overman—OEM relationships continue to be an important part of TAKK’s business approach. OEMs are obviously a source of reoccurring larger volume business, but they also provide a perfect channel to introduce and demonstrate the effectiveness of our products to the end user when new machinery fitted with our equipment is purchased. Retrofits will remain a vital focus of our strategies since OEM trends are to cut cost by eliminating accessory items, leaving the purchase of these items to the end user. Also, the end user often times is more likely to purchase higher performance accessories which provide more positive results to protect his machinery investment.
pP: With more and more use of film substrates, do you see more opportunities for growth?
Gibis—We definitely see great need for static control and web cleaning systems. In fact, this wide range of substrates is creating a need for technology advancements. We have many customers who print on paper-based substrates who are also doing more and more work on films. This has created a need for more advanced static control devices as well as a “Hybrid” approach to web cleaning. The Doyle “Hybrid” web cleaning systems offer both “Multi Modal”™ vacuum systems (for paper-based products) as well as advanced contact roll cleaning technology. This approach enables the end user to select the technology that is best suited for the substrate he is printing on, or use both in tandem. By employing both technologies, the resulting cleaning performance is at its peak.
Fyffe—Business opportunities for static control will continue to grow. However, I don’t think the bulk of growth will be seen because of the greater use of film substrates, but by the increased quality control and safety standards that are now being expected by our customers. Our converting and printing customers are being held more and more accountable by their customers to supply them with a clean, high-quality, static-free product.
Perry—Yes. Insulative materials cause the most problems for printers.
Patterson—Without doubt, the use of film-based substrates raises the need for static control equipment and subsequently, web cleaners. As film material is unwound, or passed over a moving roller, the static charge will increase, which in turn attracts particles which will affect the printing process.
Overman—With an extensive range of film substrate products made of polystyrene, polyethylene, polypropylene, and adhesive copolymers being used in the industry, the incidence of static interfering with production flow, creating quality impairments, and causing the attraction of contaminants continues to rise, making static elimination/web cleaning equipment imperative from both a cost and quality-of-production standpoint.
pP: Will RFID converting stimulate growth in the static control arena?
Gibis—Yes!
Fyffe—RFID has helped to force a rethink of how static control works. Because of RFID we need to better control and monitor the ionization performance of equipment.
Perry—Possibly. Increased use of RFID will require manufacturers/printers to be more aware of static electricity and static control equipment, and have a better understanding of how to use it to protect their production speeds and yield rates. As applications become more sophisticated, so must the equipment used.
Patterson—The RFID process is still in its infancy but as it is a high-value process any benefit to increasing yields through static and particulate contamination control must be considered. As the RFID process moves closer to printing the circuits and active components onto the film base, it will be critical to minimize static and contaminants on the web.
Overman—Yes, RFID converting has already had an initial positive impact on selling opportunities for TAKK and likely the industry at-large. Indeed, the race is on in our industry to leverage existing static control expertise toward the needs and applications of the emerging RFID converting sector.
pP: How have you tailored your products to meet the needs of RFID converting for package printers?
Gibis—Our technology is ideally suited to meet all the current and future needs of the RFID market.
Fyffe—The latest development by Meech has been the creation of our Model 986 DC Feedback System. The unique feature of this system is that a sensor bar is positioned after the ionizing bar to measure the residual charge on the web.
This system has been developed to:
• Monitor and display the performance of the associated ionizing system;
• Feedback the results to the DC controller so that its outputs are adjusted to optimize the systems static neutralization performance;
• Provide outputs and alarm signals for data logging of the ionization systems performance.
Perry—The challenge with RFID is understanding both electronic and industrial static control requirements, and having the experience to apply them properly so that the chips/tags are not exposed to dangerous electrostatic fields. Simco manufactures both electronic and industrial ionization equipment, and we have the application experience to support them.
Patterson—We have introduced a simple, easy-to-fit single-sided web cleaner (SL-NWL) that can be fitted at the critical stages in the process. We’ve also introduced an ionizing blower (Hurricane 300) and an extended range static bar (BR4400).
Overman—We have assembled a focused group of products such as Long Range Shockless Pulsed DC Ionizers, High Performance AC Ionizer bars, and Wide Area AC Ionizer blowers to meet the challenges RFID converters are facing. All of these units are engineered to provide balanced ionization output, which is an important factor when handling some RFID tags. Specifically, our IonStorm XR 2 has been designed to emit ionization up to 36” to a target surface. In addition, it has variable polarity and voltage output to control even the most challenging static issues in RFID converting.
pP: How do you view the general business climate for static control/web cleaning suppliers to the package-printing market? How much of a threat is overseas competition?
Gibis—The package-printing market has and will continue to be challenged by dust issues due to the wide variety of substrates they print on. Static control/web cleaning suppliers such as ourselves are continually striving to provide cost-effective solutions that drive up profitability for printers. Those that accept the challenge of developing new technologies for this ever-changing market will always be in demand. Being a U.S. manufacturer, we do see overseas competitors focusing their attention on this large North American market. Competition obviously is important because it motivates us to concentrate on improving our products and maintaining our position as a market leader.
Fyffe—I think that the static/web cleaning suppliers will all continue to grow over the coming years. The industry is just demanding a higher quality product. Those package printers that want to compete will need to continually update their static control and web cleaning methods in order to stay competitive.
We are beginning to see a rise in overseas competition. However, a majority of these competitors seem to be focusing more on the copying of successful products, as opposed to developing new or improved products that will help our customers and fulfill unique needs.
Perry—Packaging requirements have changed over the last ten years; the old brown box went from strictly product security, to product security and product advertising. If you consider how people shop today, products must stand out on the shelf, among a sea of products, in a huge mega-store. As such, I think the 3 percent growth projections in 2007 for the packaging industry are realistic and should hold opportunities for static control and web cleaning. Foreign competition has been increasing, but technical experience and product support are imperative for most industrial customers.
Patterson—The main impact from overseas is the production and supply of low-cost, low-quality products. The sour taste of poor performance lingers long after the sweet taste of cheap prices.
Overman—From our perspective the business outlook is positive and we’re seeing significant growth opportunities for static controls/web cleaning solutions in the packaging-print markets due to the continuous development of unique packaging substrates, inks, and ever-increasing machinery production speeds. In many cases, these developments necessitate the need for best-in-class static control equipment solutions. Secondly, we definitely recognize that we are competing on a global basis for some opportunities. Having said that, we are steadily creating international partnerships and alliances to give ourselves a more competitive advantage to further expansion into these developing markets.
pP: What opportunities do you see in overseas markets?
Gibis—Doyle Systems has seen a dramatic rise in business in its overseas markets. This is due to our technology advancements and our ability to deliver market-leading products that impact the bottom line by increasing quality and productivity.
Fyffe—We have recently seen a dramatic increase in demand from Mexico and other South American and Latin American companies. The costs of labor in these countries is considerably less than in the U.S. so we have been seeing a dramatic increase in material coming to the U.S. from these countries.
However, as these materials are destined for U.S. companies, they are once again, being required to be of higher quality than in the past. This means that the material must be cleaner and more static free than what was previously provided.
Perry—Packaging projections for 2007 in China are significant: flexible packaging, 15 percent; label market, 20 percent (pressure sensitive). The current base materials breakdown in China is 90 percent paper and 10 percent film, but future requirements point to film as the number one packaging opportunity worldwide. So, yes there are overseas market opportunities.
Patterson—U.S.-made products are still considered the best quality, so we anticipate growth in overseas markets.
Overman—One of the key marketing opportunities are in emerging industrial countries. Static control/web cleaning manufacturers have yet to establish significant bricks and mortar operations in these countries. Therefore, exporting of static control/web cleaning equipment into these industrialized areas is growing.
pP: General comments.
Gibis—We believe that there is substantial room for growth in the package-printing markets for forward thinking market leaders willing to take on new challenges. We find that understanding the needs of our customers and matching a custom-engineered solution (not taking a cookie-cutter approach) usually results in a highly satisfied customer. Companies that have limited, “off-the-shelf” solutions typically can only partially satisfy their customer needs, which results in negative view of all companies who offer static control/web cleaning solutions.
Fyffe—Static control is more of an art than a “cookie-cutter” solution. One particular product will work for one application but not necessarily another. It is very important to consult with a static control specialist whenever possible. By talking to somebody that has a great deal of application knowledge, it will be much easier to solve specific static-related problems correctly, the first time.
Another point that is often overlooked, is that it is not necessarily important to remove the static electricity everywhere on a production line. It is best to just focus on the area where static electricity is causing you the most problems. By focusing only on the problem areas, we can effectively solve the problem with as minimum a cost to the customer as possible.
Perry—Packaging may be “the” bright spot in 2007.
Patterson—Through mergers, acquisitions, and consolidations the market players have dwindled. Those that are left to serve the package-printing industry have to provide standard and innovative solutions for both static and web cleaning process problems.
Overman—The static control/web cleaning industry is experiencing a tremendous shift in customer expectations and demands. These change have driven our industry to increase its quality of product, effectiveness, and development of new technologies. We believe this trend is likely to continue. Thus, we are focusing on listening to the package-printing industry and continuously improving or innovating our product mix to meet and exceed the market demands of the future. pP





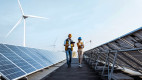