The Science of Doctor Blades
A review of the top issues concerning doctor blades.
THE ARTISTRY OF doctoring the doctor blade is giving way to science. Tom Allison, president of Allison Systems (Riverside, N.J.), remembers when he used to ask his dad what the press operators were doing as he watched them prepare the doctor blade for printing. After hushing his son, Allison's father would say, "Pressmen are frustrated artists; each one has his own 'pallet' of special things he feels that he alone can do to make 'great art' come off the press."
Where once true—when the performance of the doctor blade depended solely upon the operator's set-up—now stronger blade holders, higher quality blades, and blade monitoring software offer printers the opportunity to turn doctoring into a near exact science. Yet like any scientific process, there is room for error, and error means downtime, waste, and an inferior print job, said Johnny Stamey, technical product manager at Max Daetwyler (Huntersville, N.C.).
pP examines the most prevalent doctor blade mistakes and ways to prevent these costly errors.
Flexography
Many doctoring issues in flexo have something to do with excessive pressure on the doctor blade. Scoring, premature blade wear, and blade wave—the top three flexo doctor blade problems according to industry suppliers—can all be corrected, to a degree, by decreasing the pressure on the blade.
Anilox scoring
Cause: Scoring not only mars a print job, but also permanently damages the surface of the anilox roll. The problem usually occurs as a result of excessive pressure on the doctor blade, causing the blade to trap insoluble particles and damage the anilox. Over time, explained Bobby Furr, technical product manager for HarperScientific.com®, a division of Harper Corp. of America (Charlotte, N.C.), "Material from the doctor blade goes back through the ink train, lodges up behind the doctor blade, and starts grinding on the anilox roll." The anilox cell walls are ripped apart by the trapped material—such as wear debris from the blade or ceramic pieces from the damaged anilox—and a groove is formed in the roll. "Most of the time it goes undetected until the line starts to appear in the printed substrate, and then it is too late," Furr said.
Solution: There are several precautionary measures printers can take to prevent scoring. Ensuring that the roll is thoroughly lubricated before use with a metal or steel blade is one way, said Deborah Camacho, marketing manager at Harris & Bruno International (Roseville, Calif.). "Scoring problems are best alleviated with the use of an automatic system that triggers the ink or coating to fill the chamber prior to activating the rotation of the anilox roll," she said.
Furr and Benton Graphics (Trenton, N.J.) Vice President David Ritz, advise using strong magnets and ink filters in the inking system to capture blade wear particles. During a case study conducted by HarperScientific®, Furr was surprised by the drastic affect a magnet had on an enclosed chamber system. Water was simulated as ink pumping out of a five gallon bucket, and "within an hour of run time, the water in the bucket had turned completely gray," Furr said. "We then took a rare earth magnet and installed it in the bucket. Within a matter of minutes, the water turned back to its clear form. What this proved was that if a magnet is not being used within an inking system, the inks, plates, substrate, and the anilox roll will be effected." Rich Coleman, vice president of Flexo Inking Technology (Sellersville, Pa.), agrees. "Every enclosed chamber we manufacture today addresses each one of those problems. We control the pressure, not the operator. We now use less than 12 lbs. of pressure, and maintain it as the blade wears. Combined with blade clamping that ensures that even thin blades are held straight, scoring is preventable."
Premature blade wear
Cause: Excessive pressure on the doctor blade can be blamed for premature blade wear, as can poor quality or improper blades, and a rough anilox surface, said Stamey. "When running a Lamella tip blade, the thinner the tip, the faster it will wear on a coarse anilox," he said. Or as Ritz said, "The coarser the engraving, the thicker the blade tip needs to be."
Solution: According to Ritz, hard-coated or thicker-tipped blades will decrease the wear on coarser rolls. However, printers can prevent many problems by buying the right kind of doctor blade for their operation. "Using the very best quality steel material, proper storage, and giving a detailed description of your exact process and expectations when asking for a blade type to be recommended [will usually correct printing problems]," said Steve Wilkinson, president of ARC International's (Charlotte, N.C.) West Coast Division. "In most cases a prehoned blade will not only eliminate many of the issues, but is safer for the operator."
Blade wave
Cause: There are two types of blade wave: the first is caused by dirty clamp surfaces in the blade clamp or a wavy clamp assembly; and the second is the result of uneven wear along the blade tip, caused by excessive pressure, bad or dirty blade clamp surfaces, or by uneven ink distribution in the chamber, said Ritz. There are other causes of blade wave, said Wilkinson, including use of improper blade material, incorrect alignment of the blade or chamber, improper or lack of ink filtration, and abrasive ink pigments.
Solution: "The design of a good doctor blade chamber should minimize or eliminate blade wave," said Coleman. "The problem can be very expensive, and a chamber design that doesn't allow it to happen is one solution." Ritz advises, "The operator should always take a look down the blades to make sure they are straight after being installed in the chamber."
Gravure
The doctor blade is a "mission critical" part of the gravure press, said Allison. The slightest glitch in the doctor blade system can cost a printer a lot of money. Yet, even the smallest error can create issues like hazing, streaking, and blade wear—the top three gravure doctoring problems named by industry insiders.
Hazing
Cause: Hazing is "typically the result of low doctor blade angles," said Ritz. Low wiping angles of less than 55°, he explained, cause the blade to "hydroplane" over the gravure cylinder, leaving too much ink in the non-print areas. In some cases, the existing friction level between the blade and cylinder may result in hazing, and may call for a new blade. "When hazing appears, most printers increase the pressure on the doctor blades, and the hazing disappears, but only for a short time, and then it's back," said Ryan Platt of FLXON, Inc. (Charlotte, N.C.). "The reason it reappears is because as blade-to-cylinder pressure increases, so does the contact area, and the more contact area the more friction." Increasing pressure on the blade is also a short-lived fix because "more pressure drops the contact angle even further," Ritz said. "For a few minutes, the increased pressure stops the haze due to the blade creating a new sharp corner against the cylinder. After the blade wears into this new angle, the contact patch increases and the hazing returns often worse than before."
Solution: Knowing what kind of doctor blade to use for each print job significantly decreases the chances for hazing. However, the key to getting rid of hazing is maintaining the blade angle between 55 and 65°. Allison explained that a recent Six-Sigma™ waste analysis study conducted at a gravure plant reported that print waste due to inking and doctoring related problems was found to vary from 3 percent to 65 percent for the same product on the same press depending on which operator was running the job. "By eye, it's not hard to make an angular error." Software, like Allison Tech Doctor Blade Set-Up, takes the guess work out of the operator's hands, displaying the angle of the blade and if it's correct for the cylinder configuration.
Streaking
Cause: Similar to hazing, low blade wiping angles present the perfect opportunity for streaking too. Most often, a low doctor blade angle allows insoluble particles—like chrome particles and dried pigment ink—to get trapped under the blade, preventing ink from being applied to the cylinder in that area, said Ritz.
Solution: Quality blades, and the use of ink filters and magnets can remedy streaking. Angle analysis is also important. "The steep angle [of 55 to 65°] allows the ink to flush out all of the insoluble particles behind the blade and does not allow them to get trapped under the blade causing damage to the blade, therefore, eliminating streaking," said Stamey. "Using filters and magnets will help to thoroughly eliminate the hard, insoluble particles, which cause blade damage."
Blade wear
Cause: Blade wear is caused by several factors, including improper blade setup, quality of the cylinder, quality of the blade material, and the expertise of the operators, said Platt of FLXON. While the quality of blade material has increased over the years, accurate blade setup and high-grade blade holders are essential for preventing wear.
Solution: Increased blade angle should help decrease the wear, Ritz said. "Low doctoring angles make wear worse because more pressure is needed to achieve a clean wipe at low angles," Ritz explained. "The higher the contact angle, the less this wear is."





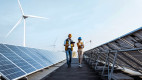