
While all segments of the packaging industry are growing, the flexible packaging market represents a major growth opportunity – both for converters already in that space and for those seeking to expand their capabilities. In addition to the ongoing trend of products traditionally packaged in rigid formats transitioning to flexible packaging, the latest in flexographic printing technology has allowed flexible packaging graphics to reach new heights.
On Tuesday, Nov. 28, packagePRINTING hosted a webinar, “How to Create Fantastic Flexible Packaging,” sponsored by Paper Converting Machine Company (PCMC). The webinar featured two flexible packaging experts — Joe Kubasiak, flexible packaging market manager for Wikoff Color Corporation and Ken Pavett, CEO of Flexografix.
Kubasiak’s presentation focused on optimizing the printing process to achieve the best results. He outlined all of the key components of the flexographic process and what needs to be considered prior to implementing these components in the creation of a flexible packaging application.
Specifically, Kubasiak detailed the questions surrounding a packaging application that converters need to answer before deciding on what ink, anilox rolls, anilox cleaners, plates and mounting tapes to use.
When assessing inks, he explained that, among other important details, converters need to strongly consider what the end use of the packaging application will be. For example, if the product is a bag that will largely be stored outdoors, the inks being used may require fade-resistant qualities. Food packaging or shrink sleeves on the other hand, may need to utilize inks that have their own specific attributes for those applications.
Kubasiak also stressed the importance of proper anilox roll selection in printing flexible packaging, referring to anilox rolls as “the heart of your press.” Specifically, he detailed the differences in the types of anilox rolls required to print large applications with heavy color laydown, such as a dog food bag, versus applications that may require screen work or fine reverses.
To provide a specific example of a packaging application that utilized flexographic printing to achieve high-quality graphics, Pavett detailed a house job Flexografix helped PCMC produce. Pavett referred to this job as, “a culmination of cutting edge graphics, plate technology, imaging technology, screening technology and press technology to get the best print results.” He explained that in producing this piece, PCMC had two specific goals it wanted to achieve — a premium print result and the application of advanced technology to compliment the challenging design that PCMC had intentionally implemented.
The end result was printed on a PCMC Fusion C central impression flexo press, and Pavett also detailed the substrate, stickyback, plate screening, plate imaging and exposure, plate material, anilox rolls, inks and press speeds utilized in this specific job. In particular, Pavett discussed why the use of Hamillroad’s Digitally Modulated Screening played such an important role in successfully completing this job.
For more on How to Create Fantastic Flexible Packaging, sign up to view the full webinar on demand. To check out all of packagePRINTING's educational webinars, click here.

Cory Francer is an Analyst with NAPCO Research, where he leads the team’s coverage of the dynamic and growing packaging market. Cory also is the former editor-in-chief of Packaging Impressions and is still an active contributor to its print magazines, blogs, and events. With a decade of experience as a professional journalist and editor, Cory brings an eye for storytelling to his packaging research, providing compelling insight into the industry's most pressing business issues. He is an active participant in many of the industry's associations and has played an essential role in the development of the annual Digital Packaging Summit. Cory can be reached at cfrancer@napco.com

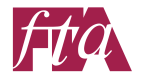
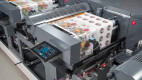

