The Expanding Reach of Narrow Web

Historically, narrow-web printing has typically referred to print widths of approximately seven to 13˝, but of late, converters are exploring wider options, with many increasing up to 24 to 27˝.
Several recent trends have taken shape with flexographic presses, primarily for labels and flexible packaging, that support this. For example, production runs have decreased in length, requiring shorter and more efficient press changeovers, and more producers are looking to incorporate digital print capability in order to expand market presence while capturing a more diverse body of work.
Additionally, many label printers are looking to expand into flexible packaging, so in addition to considering wider-format presses for labels and increased output, they are also exploring press capability for printing film, which will then be converted into flexible packaging formats.
It’s no wonder more narrow web press manufacturers are now developing wider presses to satisfy the demand.
Paper Converting Machine Company, headquartered in Green Bay, Wis., is among the press manufacturers offering a mid-web in-line press, the PCMC ELS-MAX, and several wide-web CI presses.

The control panel for the ELS-MAX flexographic press from Paper Converting Machine Co. Image courtesy of Paper Converting Machine Co.
“The ELS-MAX has taken technology from both in-line and wide web CI presses and combined that technology to produce a fast changeover in-line press that holds extremely tight register,” explains Rodney Pennings, director of sales at the company. “Printers will save up to 50-75% in both waste and setup time by having the capability to store and recall virtually every setting on the press. Stored jobs can also be shared between multiple presses with just a touch of a button.”
The ELS-MAX is rated to run solvent ink along with PCMC’s standard water-based and UV inks, and offers the ability to quickly change press parameters to make it run extremely efficiently on many types of material.
“Because of the broad print and finishing capability of the design, printers are able to utilize this single press platform to produce a wide variety of product to serve various markets,” Pennings says.
Digital Impact
Paul Teachout, business development manager, narrow-web at Anderson & Vreeland, a Fairfield, N.J.-based supplier of a variety of flexographic printing products and solutions, has been closely following the trend of printers seeking out wider presses.
“I consider narrow-web to be less than 24˝, and it’s gone through some great growth,” he says. “Obviously, it’s been tremendously affected by the proliferation of digital printing, where we’ve seen just because of the proliferation of SKUs, and the demand for quick turnaround, less inventory on a brand owner shelf, and they want things to be able to turn faster and more often.”
Last year, market intelligence firm AWA was predicting 15% of the throughput of the market for narrow-web was going to be digital, Teachout notes, but with the COVID surge and store shelves emptying, many converters reported as much as 25% of throughput was done through digital.
“Just through the last 18 months, we’ve seen more than the normal proliferation of the digital journey, and it actually accelerated it,” he says. “I think that’s going to continue to grow as well. Obviously, the hybrid solutions for narrow-web, being both a flexographic and digital solution combined with full finishing is going to have a major effect going forward, where people can take advantage of that triple threat and allows them to increase their efficiencies overall.”
On the operational side, Teachout has also seen the COVID experience accelerating the automated workflow, where people can now more often review a digital catalog, place the orders, and do all the pre-flight online, eliminating the need for an in-person press approval.
Sustainability is another key trend in narrow-web flexograhy that Teachout says is still top-of-mind for printers and converters.
“There’s a lot of plants that we’ve seen over the years that are winning environmental awards, that are going to landfill-free operations, or solar- or wind-powered operations, or creating new opportunities for their brand owners with more sustainable packaging, either by reducing the size, or reducing gauge of materials,” he says.
Meanwhile, Teachout adds that from a technological perspective, narrow-web printers will likely continue to operate both flexographic and digital equipment. With automated procedures and run lengths optimized to the proper equipment, he says converters can efficiently and effectively produce multiple types of jobs.
“Going back to conventional flexo, I don’t mean by any means that digital will overtake flexo,” he says. “I think the two complement each other very, very well. And I think tomorrow’s factory of the future is going to have a mix, if not 50/50 of conventional equipment and digital equipment, so the converter can choose the most efficient production method for that particular product mix, or demand that they currently have.”
For instance, if there’s a long run of 500,000 labels, he expects that to be run on a conventional press where a printer can get maximum speed and throughput. But if there are 20 jobs of 50,000 each, or less than that, he sees those running on a hybrid press or digital solution because they tend to run slower, but changeovers are much faster.
Today's Flexo Demands
All Printing Resources (APR) is a flexographic solutions provider based in Glendale Heights, Ill., that specializes in flexo printing supplies, flexo printing equipment, and training for flexography.

A printing unit on the PCMC ELS-MAX, a mid-web in-line flexographic press. Image courtesy of Paper Converting Machine Co.
Doug Bartlett, APR’s business development & technical representative, notes that narrow web continues to be strong, and has evolved with higher quality print, more intricate applications, and embellishments. Additionally, it’s seen much tighter tolerances and higher speeds, and in recent years, integration with digital for increasingly longer runs.
“What I see is more demands on the narrow web flexo printer to be more consistent with print quality and color management,” he says. “Printers can now have an additional window into their process with color management tools that will not only satisfy their customers, it will make them a better printer. Integration of digital with hybrid presses causes more challenges for narrow web printers — quality and consistency is what the brands are expecting.”
In flexo printing, this has resulted in more demanding print requirements along with higher color consistency expectations. Bartlett notes flexo is also playing a key role in hybrid digital applications for coatings, laminations, cold foils, and opaque whites.
Still, he notes, wider presses allow printers to be more efficient with materials, gaining an extra lane or two which can dramatically increase productivity. Bartlett is seeing it mostly used for complex high-end labels plus shrink sleeves.
“For mid-size and long run work the press width can really be critical to profitability,” he says. “More press manufacturers are developing wider presses because of press width, material efficiency, increased productivity, and profitability.”
Making the Transition
In-line printing offers many advantages when it comes to saving time and money. The versatility of an in-line press allows one operator to do the work of several, and it won’t require as much floor space and various off-line equipment.
Today, many traditional narrow-web label printers are using this equipment to grow into flexible packaging.
“Run lengths are getting shorter, making quick changeover critical to profitability,” Pennings says. “The ELS-MAX is perfect for label printers that want to transition into flexible packaging. The ELS-MAX is designed around accessibility, which results in quicker changeovers compared to CI press platforms. Its Flextreme dryer and register control help optimize production efficiencies.”
Teachout says that by expanding to presses in the 22˝ to 40˝ range, narrow-web converters can venture into the growing segments of shrink sleeves, pouches, and some non-traditional labels.
“You don’t see a lot of 28˝ presses running labels, because if you’re going to run labels, that means you need diecutting and converting, and that becomes very, very costly on a 32˝ press just because of the size of the tooling, and the weight, and then the size of the equipment and the cost of production equipment,” he says. “Now, traditional label presses, under 24˝ will have full printing and converting capabilities, where mid-web presses are usually going to be more roll-to-roll for flexible packaging.”
The industry continues to evolve, both in expanding product mix and in pursuit of automation, given the difficulty many producers have in finding qualified operators and other support personnel.
“Press manufacturers who maintain a presence on the leading edge of development to meet these changing needs are going to be most successful in helping their customers remain profitable and achieve growth,” Pennings shares.

A graduate of the University of Miami, Keith Loria is a D.C.-based award-winning journalist who has been writing for major publications for close to 20 years on topics as diverse as healthcare, travel, and tech. He started his career with the Associated Press and has held high editorial positions at publications aimed at entertainment, sports, and technology.




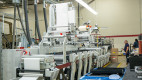
