The Answer for Static Control
Suppliers of static control systems have answered their customers call for enhanced performance, longer neutralizing ranges, and system monitoring.
STATIC CONTROL AND web cleaning go hand in hand. The build up of a static charge on any moving web will not only hold particles of contamination to the surface, but will also attract more contamination to join the party. Eliminating static build up is a big first step in keeping a substrate clean.
This is even more important today as printers are running faster speeds and more film substrates. Faster speeds can cause an increased build up of the static charge, while plastic films, being non-conductive, can build up and hold an even larger charge than more conductive substrates such as paper and foils.
Contamination on the substrate surface can result in a host of quality problems such as printing defects and coating and laminating issues. These problems can cause increased waste, or worse yet, dissatisfied customers. In addition, a build up of static on the web can pose a safety hazard to operators if they come in contact with it.
New technology advances
According to Mike Oldt, general manager for SIMCO Industrial Static Control, static bars are the most commonly used types of static control devices used in the packaging and converting industry. Except for the important development of "shockless" static bars from "hot" devices to address safety concerns, up until the mid '90s, there were few technological changes.
"At that time, several versions of bars with improved performance (longer range, higher output bars capable of handling higher web speeds and more difficult applications) came to market," observes Oldt. "Monitoring of static bar output also started to gain importance, especially with larger manufacturers with tight quality control standards."
Oldt says that these "new technology" products have caused a "dramatic shift in the style of static bars being sold by SIMCO. In 2000, these types of products accounted for less than 5 percent of SIMCO's static bar sales. This year, they will represent nearly 50 percent of sales." He lists PerforMAX 3, Blue Bar, and True AC as SIMCO products falling under the banner of new technology offerings.
The older technology products are not completely out of the picture. "They are especially popular with machine builders, due to lower cost, and users with less demanding applications. I expect that they will continue to be popular for many years," Oldt predicts.
What customers are asking for
With users' appetites for new technology advancements appropriately stimulated, Oldt says that SIMCO's customers are continuing to ask for three major features: higher performance static elimination, static elimination at longer distances, and the ability to monitor the operation of the static eliminator.
SIMCO has answered its customers needs with its PerforMAX 3 static control system, the TrueAC power supply, and its Blue Bar static bar. PerforMAX 3 has an extended range performance of 2˝ to 10˝ from webs and up to 20˝ on winders. It can also neutralize charged materials at speeds up to 2,500 fpm, depending on conditions.
It offers an array of features for monitoring static neutralizing performance. These include a bar graph display showing percent neutralizing efficiency, a setpoint-selectable clean bar indicator, and an indicator light and automatic shutdown if a fault occurs. PerforMAX 3 can also be configured for use in hazardous locations or with an optional computer interface and software program for remote monitoring and data acquisition.
SIMCO's TrueAC is a self-monitoring power supply designed for use with the Blue Bar static bar. This system can also handle static neutralization on materials running up to 2,500 fpm and provides monitoring features such as bar performance range indicator; clean bar indicator; remote display capabilities for clean bar, fault, and service; and arc detection circuitry.
Tobias Wagener, general manager for Haug North America, lists additional capabilities desired by his customers as maximum safety when dealing with high voltages and flexibility in terms of product configuration. To address these concerns, Haug has developed the X-2000 safety connection system that effectively grounds the ionizer before any high voltage connection is made. In addition, several new connection options developed by Haug allow one power supply to deliver high voltage to several ionizing bars to eliminate the requirement for multiple cables and power supplies.
Wagener also understands the customers' needs for system monitoring. "A question that we hear a lot from customers is 'How do I know if my static control system is working properly?'" Haug now offers several power supplies, including the S-Line SC/RLC, which provide a warning light to indicate if a malfunction occurs. Wagener believes this approach provides a simpler, more cost-effective solution for many applications vs. monitoring performance with electronic devices and computers.
Matt Fyffe, general manager of Meech Static Eliminators, believes the need for higher performance static control is being driven by intense competition. "As the converting and packaging industry gets more competitive, our customers are required to keep an ever-increasing high level of quality control."
According to Fyffe, Meech's customers are requiring long-range static neutralization without the use of air. In AC controlled static systems, compressed air or fan-driven systems are sometimes used to assist the neutralizing ions to obtain a longer range. A drawback is that the air-assisted systems can sometime blow contamination back onto the web, says Fyffe.
To provide the required longer-range static control, Meech has developed the Pulsed DC 976 shockless system that also uses high voltage, but at a much lower supply frequency. It provides the ability to control the distance between the ions to change the effective range of the bar from the substrate. This system provides a range of up to 42˝ without the use of air.
An added benefit of the Pulsed DC system is that the ion output can be controlled. "If the static charge to be neutralized is known to be negative, the operator can adjust the ion output of the Pulsed DC system to create more positive ions to neutralize the negative charge on the material," says Fyffe.
TAKK Industries also offers a pulsed DC ionization system. "Often, positioning a static bar in close proximity is not possible, or blowing ionized air poses the risk of introducing further contamination," says Sales Manager Terrance Clark. The TAKK Ionstorm pulsed DC ionization system provides an extended range of up to 36˝ and is available in standard lengths of 10˝ to 100˝ in 10˝ increments.
The Model 3700 Controller used with the TAKK Ionstorm can be adjusted to handle high static charges in either polarity, or set to balanced outputs for most applications. The balanced output can be set to 80:20 in each polarity to meet the needs of the application.
As applications get more sophisticated and applications more demanding, companies such as Meech are using higher levels of technology to provide static control solutions. "One of the latest developments in static control is the ability to have closed-loop feedback systems," reports Fyffe. "This is a very niche area where some converters require their ionizing equipment to actually 'read' the static charge on the web and to adjust itself to compensate for the static charges. While these types of systems are quite costly, they are finding a home in the high-end converters that need to have as low residual charge as possible."
Suppliers of static control systems are using state-of-the-art technologies to provide enhanced solutions for the age-old problem of static elimination. This trend will continue to provide package printers with a wealth of options to help solve their static control problems.
By Tom Polischuk
Editor-In-Chief





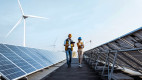