A Sticky Situation

What good would print be if the ink didn’t stick to what it’s supposed to? Strong ink adhesion ensures a printed item maintains its graphical integrity, which is essential when it comes to packaging where appearance is everything.
However, with the rise of inkjet printing, not all substrates are fully compatible with this new technology. Fortunately, there are preemptive procedures that can help ink stay where printers and brand owners want it.
Challenging substrates
As with conventional printing processes, some of the more difficult substrates for inkjet ink to adhere to are some of the most common materials used in packaging. Among these challenging substrates are plastics like polyester and polypropylene, plus metal and glass.
According to Paul Edwards, vice president of inkjet technology for EFI Inkjet Solutions, the best way for an ink to stick to a substrate is if it actually dissolves directly into that material.
“What happens in that case is that when something is dried and cured, molecules of the two materials intertwine and really become a hybrid material.”
One of the more difficult surfaces to make that happen with is polyester, Edwards details. However, there are ways to improve adhesive properties that the substrate manufacturer can implement.
When dealing with polyester, Edwards says a coating can be placed onto the surface of the material that is attracted to both the polyester and the ink. This coating, called an intercoat, provides a buffer between the ink and substrate.
“It transitions from one chemistry to another chemistry because the intercoat has characteristics of both the ink and the substrate,” he explains. “Often, it’s used as a prime layer to improve adhesion of all sorts of different materials to a polyester.”
Corona treatments
In some cases, rather than adding material to a substrate’s surface, adhesion can be increased by altering the properties of the substrate. Frequently, this is done with corona treatments.
Heather Rockow, UV business development manager at Collins Inkjet, says printers often prefer corona treatment because it can be done inline with the printing, unlike adding a coating, which isn’t always an inline process.
“There’s some resistance to putting on a coating on something as a separate process, because you’ve probably gone to inkjet because you didn’t want separate processes,” Rockow says. “Then you’re back to corona treating or flame treating and building that into your printer or printing process.”
Edwards explains that the act of corona treating actually increases the surface energy of the substrate. By allowing it to have a higher surface energy than the ink, Edwards says the ink will then spread across the substrate and grip better to the surface, from both a chemical and physical perspective.
One drawback of corona treatment though, is that it is not permanent. For example, Edwards says if a corona treated item is exposed to air for an extended period of time, the treatment will wear off.
“If you do a roll of substrate, and you roll it up tightly, once you get past the outer layer it’s going to be pretty good for a long time,” he says. “But if you do the corona treatment and left that substrate sitting around in the air for a few weeks and then try and print it, all that surface energy will dissipate and you’ll have a problem with adhesion.”
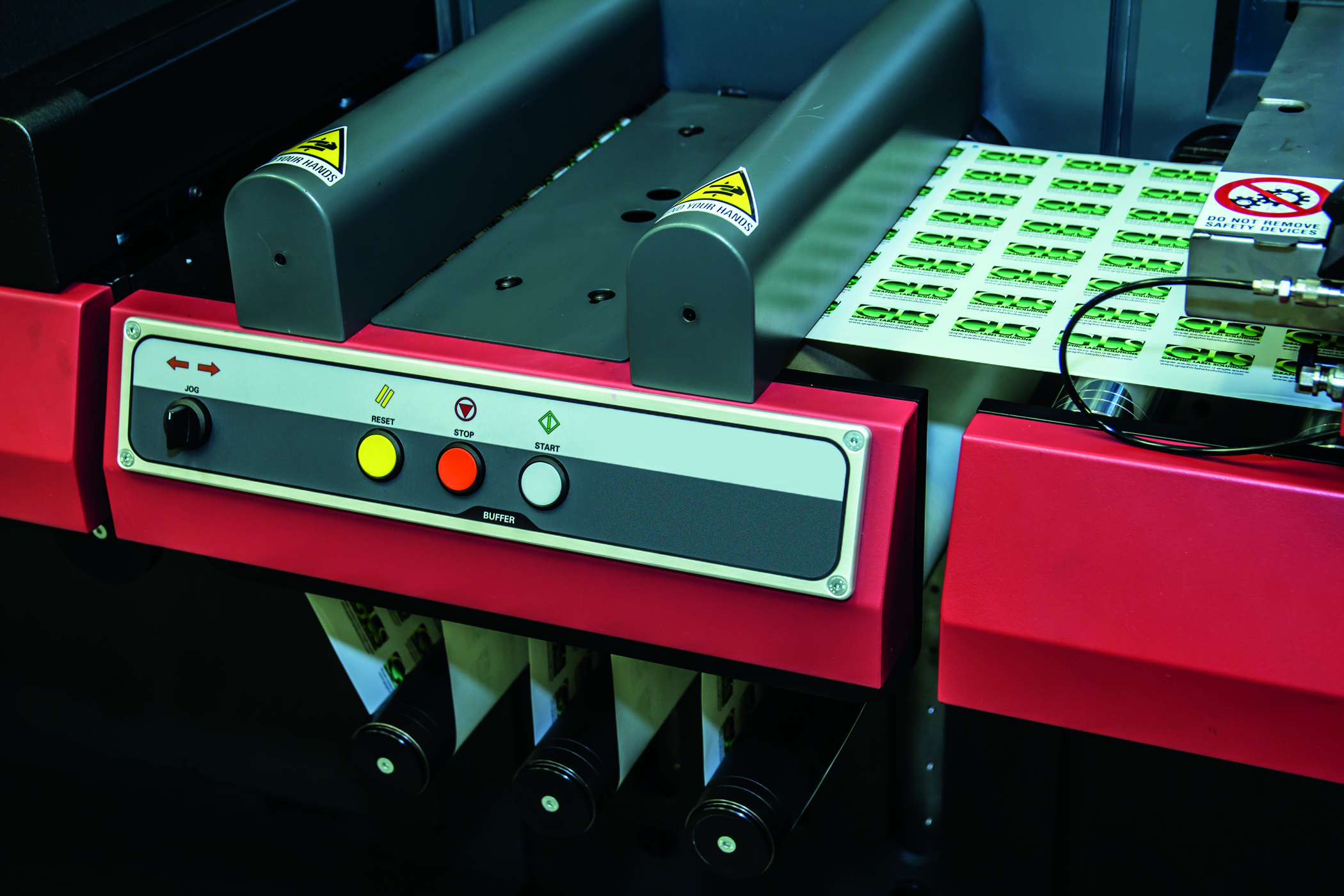
Label printing on a UV inkjet press at Graphic Label Solutions in Nashville, TN. Photo courtesy EFI.
Adhesion promoters
Because there are so many variations of ink and substrates, a variety of adhesion promoters can be implemented into the printing process. Rockow says that as an ink manufacturer, Collins Inkjet can add adhesion promoters directly into its ink.
“There are adhesion promoters that we put into the inks themselves,” she says. “That’s the magic of the chemistry. The chemists figure out what they need to put into the ink, especially when you’re dealing with the more difficult substrates.”
In addition to adhesion promoters that can be put into the ink, there are others that can be added to the substrate.
Edwards explains that these adhesion promoters can serve a variety of purposes. In some instances, the promoter can be used to change the surface energy, or it could change the chemical polarity of the printing surface. But before implementing an adhesion promoter, Edwards recommends testing it first.
With so many potential ink and substrate combinations, selecting the correct adhesion promoter is essential. “The fact that there are so many of them tells you they aren’t all the same and that they don’t all work the same way on different substrates,” says Edwards.
Don’t hesitate to talk with your ink and substrate vendors to find which are best for each application.

Cory Francer is an Analyst with NAPCO Research, where he leads the team’s coverage of the dynamic and growing packaging market. Cory also is the former editor-in-chief of Packaging Impressions and is still an active contributor to its print magazines, blogs, and events. With a decade of experience as a professional journalist and editor, Cory brings an eye for storytelling to his packaging research, providing compelling insight into the industry's most pressing business issues. He is an active participant in many of the industry's associations and has played an essential role in the development of the annual Digital Packaging Summit. Cory can be reached at cfrancer@napco.com





