Problem Solved
Dirt, dust, and any number of other contaminants can wreak havoc on a printing press. Package printers understand this well and work hard to maintain clean working environments and provide the necessary systems to eliminate contamination in their printing operations.
Key components incorporated onto printing presses to achieve this purpose include static-elimination and web-cleaning systems. With the growing use of film materials, run at higher and higher press speeds, the need to control static (a.k.a., dirt magnet) and assure that substrates are free of foreign material is greater than ever.
There are a number of companies that supply static-control and web-cleaning equipment and these companies can be an invaluable source of expertise when facing tricky static/cleaning problems. There is a good chance that they have seen similar problems that you might face and have been able to provide an effective solution.
packagePRINTING asked a sampling of suppliers to identify specific problems that they have seen and how the problems were solved.
Mark Gibis, vice president of sales, Doyle Systems
Problem—We find that the most difficult problem to solve is when a wide variety of substrates are being run on a particular press. An example would be when a press operator has to go from printing on paperboard (high dust content) to film or foil, then back to paper. This problem was brought up repeatedly by attendees at the recent Labelexpo show in Chicago.
Solution—Based on this need, Doyle Systems has developed a “hybrid” system that will handle these complex challenges. The hybrid technology includes high-intensity (shockless) static control devices to eliminate even the highest static charges, both before and after the cleaning process. It combines multimodal™ full-contact vacuum cleaning with contact roll cleaning technology. This multimodal cleaner is at its best on high-dust and paper-based substrates. On scratch-sensitive substrates like films and foils, the contact roll cleaning system will effectively clean without marring the surface. The hybrid system also provides the operator with the option of using both technologies together to bring the cleaning performance to the highest levels possible.
Michael Anderson, N. A. sales manager, MKS, Ion Industrial
Problem—A customer’s production process involved the filling of chilled yogurt into tubes, or “pops,” with a continuous tube forming, filling, and sealing process of printed packaging. A problem occurs when electrostatic charges on the packaging attracts material (usually the product itself) into the seal areas.
Solution—This particular problem was puzzling to our customer since it already was using static neutralizers on the packaging material just before it entered the filling process. We discovered that the packaging was recharging through sliding on the pop former, and just after completing the filling, strong static fields from the packaging were pulling additional yoghurt from the applicator nozzle into the seal area. We used the Virtual AC neutralization technology as its long-range bars allowed for neutralizing the full packaging -dimension.
Matt Fyffe, GM, Meech Static -Eliminators Inc.
Problem—A large extruder of expanded polystyrene foam material was running into severe static electricity issues on their winders. The accumulation of the high static charges resulted in sparking.
Because the web path continuously changes (or indexes) on winders, a standard AC bar does not have the range capability to continually remove the charge from the web as it indexes on to the winder. Since the final product was used in food-grade packaging, the customer did not want to use an ionizing air blower as it did not want to blow potentially dusty air on to the finished product.
Solution—A Meech Model 976 Pulsed DC System was -selected to remove the charges from the roll as it was wound. The Meech system achieves effective long-range neutralization due to the capabilities of the pulsed DC technology and the design of the emitter array. The system allows adjustment of both the pulse rate/frequency and the ion balance, enabling the user to control the effective range of the system for the specific application.
Because the fumes from the expanding process “out gassed” from the winding roll, there was still some concern that a spark could cause a fire. The customer also decided to use a Meech Model 976EX Long Range Pulsed DC bar.
Jay Perry, marketing manager, SIMCO
Problem—The most difficult static control issue that I have experienced was a paper application where the web was transported at speeds in excess of 4,500 fpm.
Solution—This problem was resolved with the addition of two high-efficiency AC ionization bars, at a measured spacing, to control the charge.
In general, Perry says that speed and material type are the most complicating issues for static control/web cleaning. “Some films generate significant electrostatic charges as they are being processed, and the addition of a corona treatment often exacerbates the problem,” he adds.
Jim Patterson, president, Static Clean International
Problem—In many web press applications, film substrates—especially label stock—have to be corona treated in order for ink to bond to the substrate. The corona treatment process, which uses high voltage to bombard the stock, can create imbedded charges in the film which are difficult to eliminate. These charges are sometimes called polarized charges or electrets and are difficult to detect using traditional handheld static meters. Blocking on film being wound on a take-up roll and difficulty feeding once the material is sheeted are a couple of well-known problems resulting from this condition.
Solution—For static control, sometimes a grounded passive static bar mounted over a grounded idler roll and making contact with the web is the best solution and most cost-sensitive approach. Some passive brush materials are soft enough so that they don’t scratch the web. Conventional web cleaners and the increasingly popular contact web cleaners will work as well to rid the web or label stock of dry surface contaminants. The level of cleanliness required will dictate which type of cleaning system will work well for a particular application.
Terrance Clark, sales manager, TAKK Industries
Problem—One of the most challenging problems we’ve encountered is in label printing and converting. With cut-and-stack labels, the converter typically prints on a film substrate and then diecuts and stacks the completed labels. A technique called “bumping and stacking” is used to gather the labels into a uniform stack and package them. Problems occur when static electricity—generated on the film substrate as it moves through multiple stations—causes the delivered labels to stick together.
Solution—A solution we have provided is the installation of our IonStorm XR2 Pulsed DC Long Range Ionizer. This system delivers high-intensity waves of positive and negative ions that eliminate static electricity. Immersing the layers of static-laden labels is key to solving this problem. Additionally, the IonStorm XR2’s ion polarity, voltage, and pulse rate can be tailored to suit the specific needs of the process and to optimize the effectiveness of static elimination. pP





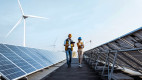