Shocking Fact of Life
Static control and web cleaning go hand-in-hand with safety, productivity, and quality in the package printing industry.
STATIC ELECTRICITY IS a fact of life for most printers and converters. So are the productivity, quality, and safety issues that accompany static and its resultant web contamination.
Static is a naturally occurring nuisance on many packaging substrates, building up as a result of the general processes of converting and printing, and aggravated by seasonal changes. The problem arises "once the material is out in the open, going from roller to roller, it becomes highly charged and pulls particles from the manufacturing environment to the film," explains Andy Grzesik, general manager of Tantec, Inc. (Schaumburg, Ill.).
Without static control or web cleaning equipment, the particles cling to the substrate, creating botched print jobs and, ultimately, waste. With the appropriate equipment, the charged substrate is neutralized, and what debris does contaminate the material can be cleaned away. The result: unmarred end products that please customers.
With the help of suppliers and converters, packagePRINTING took a closer look at three main issues converters and printers deal with when combating static: safety, productivity, and quality.
Safety first
Converter's issue: "Hop Industries has been converting PVC sheeting and Hop-Syn Synthetic paper for more than 25 years. These substrates generate a large amount of static electricity during converting processes, and static elimination units are necessary to minimize the static so that the operators will not be constantly shocked," said Robert Noetzel, the marketing director of Hop Industries Corp.
However, since adding an Ion Systems Industrial static elimination unit to its new Dusenbury slitter/rewinder, Noetzel added, Hop has been able to protect operators from being shocked, and produce rolls of product with a neutral charge that helped its customers.
Solution: In many instances, static electricity is an irritating nuisance, more just an attention-getting shock. However, machine operators can be shocked time and time again, and sometimes with serious effects. "The massive electrostatic charges which build up in reels of plastic film, may, in certain circumstances, be strong enough to throw an adult across the room when discharged," said Matt Fyffe, general manager of Meech Static Eliminators (Richfield, Ohio).
Personnel safety is a growing focus for much of the converting industry, according to TAKK Industries Inc. (Cincinnati, Ohio) Sales Manager Terrance Clark. With strict Occupational Safety and Health Administration regulations to follow, and general concern for their employees, companies take static control seriously. They have to.
"Simply unwinding a web can induce 30,000-plus volts of static charge, which will result in contamination being drawn onto it very quickly," said Mark Rollinson, Teknek LLC (Elk Grove Village, Ill.) sales manager. While the end result is a quality issue, Rollinson said, "Static control is also a major safety consideration as the charge can reach levels hazardous to operators who come into contact with the web."
Grzesik added, "[Static control] is needed to prevent operators from receiving painful shocks and having a potentially deadly reaction to receiving a shock, i.e. recoiling from a shock or falling off a catwalk into a set of large diameter rollers."
In addition to serious, harmful shocks, static electricity can be deadly around certain chemicals in the printing and converting processes. "Some printing and coating solutions are volatile solvents, and can be ignited by electrostatic discharges," explained Jay Perry, marketing manager of SIMCO Industries Static Control (Hatfield, Pa.). "These areas are generally classified as Class 1, Division 1, Group D environments by the National Fire Protection Association."
Fortunately, static control as a way to ensure worker safety doesn't have to be complicated, Clark said. "The solution can often be as simple as installing an appropriate length strand of copper tinsel or a tinsel bar across the entire web or sheet width. Copper tinsel has hundreds of small soft-copper points, which ionize air molecules and allow static charges to flow to ground through the tinsel or tinsel bar, via an earth ground or a grounded machine frame," he said. "The net effect is that the ionized air molecules 'carry the static charge away,' before it can harm operators, or damage expensive machinery sensors or components."
Mark Blitshteyn, vice president of industrial products at Ion Systems Industrial (Windsor Locks, Conn.), added, "Keeping the static levels low with long-range electrical static neutralizing bars help prevent both operator shocks and contamination. Additionally, if a winding roll is neutralized throughout the winding cycle, there are fewer static-related problems during subsequent film converting operations."
For output and quality's sake
Converter's issue: "As a converter, we deal with major static issues on a regular basis," reports Preston A. Baillargeon, PAK 2000 maintenance manager. "The static builds up in our unfinished product during the printing and converting processes. With such high levels of static, it causes our machines to run poorly, and ultimately production speeds and quality are lost.
"The main cause of our static problems is the unwinding and rewinding of our substrate during our printing and converting process," Baillargeon said.
By installing Ion Systems units on two converting lines, PAK 2000 was able to keep static in check, with one static bar located at the delivery end of their converting machines.
Converter's issue: Dust generated by paperboard stock and static has been a persistent problem for the John Henry Co., according to a case study for Doyle Systems. "As a major supplier of packaging to the pharmaceutical industry, the John Henry Co. wouldn't think of delivering a less-than-perfect job," according to the study. "As a result, it was scrapping as much as 20 percent of the printed product. Increasing yield would not only save material, but also press time and downtime, as well. And it would deliver dollars straight to the bottom line."
To increase yield, a Doyle Systems web cleaner was added to the converter's process. It worked and reduced scrap by 3.7 percent and provided cost savings up to almost $185,000 per year in materials.
Solution: For all companies dealing with packaging, output is critical and static can hinder it. "Improving productivity is the No. 1 issue right now with respect to web cleaning in packaging applications," said Peter Mariani, president of ElectroStatics (Harleysville, Pa.). "Customer complaints related to product quality and/or dust and dirt on the product, machine downtime, and scrap rates all have a negative impact on productivity and profitability in package printing operations," he said.
Productivity is also the main reason customers invest in static control technology, Mariani said. Converters and printers dealing with static often are looking to remedy mechanical and quality problems like machine jams, having to operate at slower operating speeds, operator complaints, customer complaints, or contamination. "Package printers complain that dust on their substrates creates the biggest challenge in producing a quality package," said Doyle Systems (Richfield, Ohio) Vice President of Sales Mark Gibis. "In order to maintain quality, they have to shut down their presses often due to paper and coating dust building up on the plates or blankets. This dust can cause hickeys, voids, and color variations, resulting in rejected packaging."
However, fixing static-related productivity and quality issues doesn't have to be a mind-bending or pocket-emptying experience. "Whenever contamination is a concern, air ionizing devices like ionizing air nozzles, air bars, ionizing airknives, and WebVacs become common tools for the fight to control static, and its ability to attract and hold particles," said Jim Patterson, executive vice president of Julie Industries, Inc. (Wilmington, Mass.). "Most converters and printers are familiar with web cleaners that include blow and vacuum components, sticky/tacky tapes, ultrasonic, and a host of other products that bear similar acronyms. The engineer who takes these conventional tools and uses his or her imagination will have a better chance of solving unique problems at a lower cost."
Luckily for converters and printers, there is a wide range of static control and web cleaning equipment to choose from, with most companies offering a mix of the aforementioned technology and processes. From static eliminators/neutralizers to continuous contact cleaning systems that use tacky rolls, to air cleaning systems that include brushes and vacuums, there is equipment suitable for every kind of packaging substrate.
With so many quality choices, end users need to know a few things before investing in one kind of technology. No matter which kind of system is implemented, it has to be able to penetrate the boundary layer of air—a layer of static air on the surface of any moving object, which can be more than 100 microns deep, said Rollinson. It's within this layer that contaminants cling, and where web cleaning systems need to be able to break through to successfully do their job.
There are several viewpoints concerning what cleaning systems are effective against the boundary layer. Air-vacuum systems, when used alone, are labeled as ineffective by many suppliers. Air blown across a web or sheet cannot break the boundary layer, which means it's unable to dislodge the contaminants, rendering the vacuum useless. Some manufacturers also believe that air systems do little more than blow more contaminants onto the web.
However, an air-vacuum cleaning system can be productive if used in conjunction with brushes that rub across the web or sheet, or with an ionizer that neutralizes the substrate and frees up the debris, said Clark. But, he said, "It's imperative to utilize copious levels of ionization to remove the static charges that are causing the contamination to cling. Once we achieve this, we can simply blow off the remaining contamination."
Whether a converter or printer uses an air-vacuum or a contact cleaning system, Perry said it has to be a well-designed system to ensure quality cleaning. "Well-designed web cleaners are built with static elimination equipment included to control static electricity. The system must also be capable of controlling the boundary layer of air for complete particle extraction," he said. "And the system must have an effective extraction method, such as vacuum or contact cleaning, to remove particles."
In addition, when dealing with static control, the ionizer has to be strategically located to ensure its efficiency, and should produce a sufficient amount of ionization to neutralize the web or sheet. "The longer the product remains neutralized, the less chance it has to attract particles, which means less particles from the environment will stick to the web through the entire converting and printing processes," said Grzesik.
Meech Static Eliminators' shockless Pulsed DC 976 system offers long-range neutralization, enhanced by its unique array of emitters. The system allows adjustment of the pulse rate/frequency and the ion balance.
The QuadClam, HexClam, QuadClean, and HexClean—clamshell-designed contact cleaning systems by SIMCO—can remove particles from 20 microns down to 1 micron in size from a moving web. Using contact cleaning (tacky) rolls in a nip configuration, the CCR applies from .5 to 2 psi on the web, squeezing out the boundary layer of air.
By: Kate Sharon





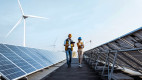