Near Miss
"Above all, plan for the unforeseen," read the beginning of a February 2008 packagePRINTING feature on offset printing. The subject of the article, Colonial Carton Company (now 3C Packaging, www.3cpackaging.com), had taken steps to ensure its customers would not see a disruption in service in the event of a catastrophe. The printer did have to put its plan into place when it almost lost its building and equipment to fire.Although the circumstances were different, M&M Printed Bag (Chino, Calif.) recently encountered a unique challenge not seen by many in the package-printing marketplace. The printer took delivery of an 8-color, 53˝ flexographic Onyx press from Uteco (www.uteco.com), and upon unwrapping the shipping carton, discovered water flowing from the press's central impression (CI) section.
Niche player
M&M Printed Bag has been in business for 24 years and located in Chino since 1990. Its facility is home to three printing presses and nine bagging machines. All its business is wide web, with presses that go up to 61˝ wide. In its 24 years, the business has experienced steady growth, and according to Ernest Taylor, CEO, has not been adversely affected by the current economic environment. "Despite the economy we're in," he says, "we are not having difficulty in getting new customers." Customer retention has also been key to the company's growth.
M&M is a niche player, according to Taylor, not fighting the "big boys" if it can avoid it. "We find those areas where customers require quality and quick turnaround." And when Taylor says quick turnaround, he means it. "I mean that's where they call on a Monday and say they're going to be out of product by Friday, and we produce it and ship it to them so they've got product on their floor by Friday." It's been that way all along at M&M. "That's the way I built the business and that's why we've got customers who have been with us for over 20 years," he adds.
Of M&M's three presses, two are Uteco units and one is a CMF. Its customers include those in the towel and tissue industry, the bakery industry, and a limited number in agriculture.
It was the company's third Uteco press that posed a unique challenge for the niche printer.
Rain, rain, go away
M&M's most recent press, a 53˝ Uteco, was assembled in Italy and shipped to its Chino facility. At delivery, "we broke the cover on it and we had water flowing out of the CI section," says Taylor. He determined the water to be rain water and immediately contacted Uteco.
"Upon hearing of the damage, and while the insurance company was being notified through the official channels, I made immediate travel plans to Chino to evaluate the extent of the damage," says Marco Verini, Uteco North America's service director. Additionally, he gave give Ernest Taylor Uteco's guarantee that it would activate all its resources to replace all the affected components, without question, as quickly as possible. The situation was also challenging for Uteco. "This is the only instance in the 10 years I've been with Uteco where we've had to intervene to such an extent on a press," says Verini. "There was nothing standard about the situation or the subsequent coordination of efforts."
Getting up and running
Uteco delivered the press to M&M in December 2008, but it was not placed into service until February, according to Taylor. The reason for the delay was the extent of the work done to return the press to its factory condition. "I won't even guestimate how many hundreds of thousands of dollars they replaced in parts," says Taylor. "But, anything that could have potential damage or rust from the water, they replaced."
Uteco had parts shipped from Italy to the Chino facility within two weeks. "They brought three people out here from Italy working on it to get it done," continues Taylor. "They just did an excellent job in correcting a poor set of circumstances."
Verini adds that involved parties quickly realized that requisitioning all the necessary components to repair the press would take too much time. Based on the initial assessment at M&M, Uteco decided to strip the necessary components (to the tune of 150,000 Euros) from a fully assembled press at the factory and air-shipped them to California. "Two crews traveled from Uteco Italy to work on opposite sides of the press for two weeks to remove and reassemble all the electrical and mechanical components, and to redo a complete checkout and start-up procedure," says Verini.
Another satisfied customer
The press has been in continuous service since the latter part of February 2009 when Uteco technicians completed repairs, and Taylor has nothing but praise for the press.
This Onyx was added to increase capacity, and to provide 8-color printing capability for M&M since its other presses are 6-color. Prior to delivery, M&M had already lined up 8-color jobs. The company incurred revenue loss, "and that was a little bit stressful," admits Taylor. But his customers understood. "We contacted our customers. They were very understanding. They placed orders with us for deliveries later so we'd be able to run them once the press got going."
When it did get going, the jobs run on it offered quality that rivals gravure, according to Taylor. "With what we're getting off this new press, it might not be gravure, but you'd better be a real authority to be able to tell the difference from a quality standpoint," he claims. "The registration is just exceptional. Once you turn it on, [the press] takes care of itself."
This quality has been flexo's story for some time. "The gap has been narrowed between flexo and gravure," says Taylor. "It's been getting narrower and narrower for the last several years… And now we have customers that had been buying gravure, and they've come over and bought from us, and they are extremely happy." pP
- Companies:
- Uteco North America





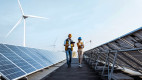