As Fast as a Speeding Press
Like any other technology, drying equipment for package printing continues to evolve. The industry changes rapidly and suppliers must keep up. The increased speed involved with today’s printing presses, driven by market demand, is one example of how drying equipment must evolve to keep up with the presses on which it is installed. Some press manufacturers, like Aquaflex (see sidebar, next page), have chosen to design and build their own drying systems. Others use dryers manufactured by OEMs.
Whichever route you choose to go when purchasing new drying equipment, there are a variety of considerations you need to keep in mind including UV vs. IR vs. air, advances in anilox roll technology, emergence of film applications, and the higher speeds and efficiencies of today’s presses.
Emerging trends
A variety of trends have emerged in the drying equipment market. Mark Hahn, VP sales and marketing for AAA Press International, states, “We see trends where converters are looking to run faster to improve throughput regardless of run size.” Dave Schommer, president of Dri-Tec, adds, “Because of the increased speeds and web widths, such as 2000 fpm at 150 inches wide, better drying methods have to be addressed. This is especially true on central impression (CI) presses where between color trap, drying has to be accomplished in a very short time before the next color is applied. The higher the speed, the less time is available.” He adds, “Higher-velocity air has helped, but is now running into the problem with non-absorbent substrates in that a dot of ink becomes distorted with the high-velocity air before trap drying. This is not desirable in process printing. Along with higher speeds, requiring faster drying, comes the need to have finer control of the dryer for the varying speeds. “Customers are looking at very fine control in some new and critical markets,” says Bob Narang, president, Radiant Energy Systems.
Also affecting drying equipment is anilox roll technology, which has “allowed converters to lay down thicker coatings for improved opacity and better physical properties,” says Hahn. “Dryer specifications require higher power levels and improved thermal delivery systems to ensure drying at higher speeds. Too little power yields poor throughput, while too much power can reduce the desired physical properties of the coating.” Again, the need to control the dryer is critical, and Hahn adds that, “Most successful systems will include some type of heat density control to deliver the proper drying power proportional to press speed.” These controls are also allowing converters to do more with one drying system. “The emergence of more film applications requires dryers to be more accurate in temperature control to dry the ink or coating but not distort the film,” he says.
Combination drying has also surfaced in some recent applications. Schommer cites one application in which an electric dryer was placed in-line prior to a gas forced-air dryer to assist in the drying requirement of the job. Another application had a gas dryer used to trap dry ink and a UV dryer to cure a UV overcoat prior to passing over an idler roll. Originally, the overcoat was to be water-based but room wasn’t available to air-dry before coming in contact with the idler.
Narang states that Radiant Energy sees combination dryers using infrared and air doing quite well. “We also have new T3 lamps, which are rated at 100 W/inch but generate energy in the medium wavelength range. These lamps were previously available in short wavelength only,” he says.
C.A. Litzler addressed its customers’ needs to improve their processes and reduce manufacturing costs by designing a combination floatation dryer. The dryer uses both convection and infrared technologies. “The use of two technologies delivers more effective and efficient heat transfer while increasing productivity and quality at reduced operating costs,” says Matt Litzler, president, C.A. Litzler. “Convection offers the steady and thorough heat-up while infrared works faster to reduce the time needed to dry material.”
UV’s impact
UV technology’s impact on the package-printing industry is unmistakable. Using UV technology is environmentally friendly and is easier on the pocketbook when considering today’s energy costs. As UV technology has captured more market share, the drying equipment market has been affected, but for the better in many cases.
“The increased use of UV technology has helped improve our business, as we manufacture combination inline UV/IR systems that use a compact UV lamp assembly in combination with a compact electric impinged-air IR drying assembly—all controlled through one operator interface,” says Hahn. “Operators can choose UV or IR for each individual station depending on the process they are running for each job.”
Schommer adds that UV technology helps in applications where room is not available between laydowns and the coating requires curing for the next application.
Energy costs have also led to UV systems being viable alternatives to traditional drying systems. According to Dave Samide, marketing manager, Prime UV Systems, “While energy costs are always a concern, the focus on these expenses is growing. With the price of natural gas on the rise, today’s converters and package printers see UV curing as an energy-saving alternative to natural gas dependent dryers that necessitate afterburners or incinerators.”
Hans Ulland, vice president of sales at Air Motion Systems, states that he has not seen a renewed focus on energy costs in the U.S., but that energy costs will be an important part of the future of UV. “Right now, the environmental benefits are enormous, so UV will become more commonplace as local environmental regulations tighten,” he says. “Energy conservation will be the next step in UV to become an even more green technology.”
More on energy
Using UV systems is not the only way to address the ebbs and flows of energy costs, and in the case of Radiant Energy, the ebbs and flows will drive different projects. “A few projects we did this year were driven by rising energy costs earlier in the year,” says Narang. “Towards the later part, the interest dwindled as the energy prices leveled off.”
Controlling exhaust temperature is one of the keys to controlling energy costs. Litzler states that “Customers are interested in energy savings, and we see more customers using variable speed drives for the fans and really concentrating on exhaust levels. The exhaust is the largest single component in the energy balance. The key is lowering the exhaust to the proper level for drying and not much higher.”
Hahn adds, “Most converters want a system that will help them control energy costs. Using impinged-air electric IR dryers does that by having the heat source close to the substrate with an impinged air delivery system and ‘auto-ramp’ temperature control to use only the amount of energy necessary to fully dry the ink or coating.”
Bottom line
A converter’s final decision on whether or not to add a new drying system will largely depend on how much you can afford to spend and the speed at which you are printing. According to Hahn, more and more converters are considering upgrading their existing older equipment with newer, more accurate drying equipment and upgraded tension controls at a fraction of the cost of a new press. He also states that 70 percent of AAA Press’s sales are to end users looking to get more out of an older press by improving drying throughput. “Adding a six- to eight-station dryer to an older press is cost-effective, as the payback is less than one to two years due to improved throughput.”
Schommer considers the room available as the critical factor. “The largest stumbling block when increasing speeds, especially with nonabsorbent substrates, is drying. It is normally not a problem when ample room is available. But floor space is a premium and will dictate developing new, efficient methods to improve drying.
The key in the end is to find a company that will work with you to build a dryer that is right for your applications and your press. In Litzler’s case, the company works with its customers to help them cope with the trends in the industry. “Litzler works with customers to design a piece of equipment that meets their needs,” says Litzler. “Knowing the customers’ wants and needs ensures a dryer to be no more or no less than what they require.” pP
A case for proprietary drying systems
Although there are various companies that manufacture drying systems, some press manufacturers also build proprietary systems specifically designed and optimized for use with their presses.
One such company is Aquaflex (Pa.). The company has had years of experience in dryer systems design, so there was no real need to seek a technology partner to create its latest generation of Aquaflex dryers. “We know the capabilities of our presses and have designed our dryers to optimize those capabilities,” says Mac Rosenbaum, vice president.
The choice of whether or not to spec out a proprietary drying system for an Aquaflex press is still left up to the customer. According to Rosenbaoun, Aquaflex will sell presses without a proprietary drying system, but developed its own to give the customer a choice. “We will install (and have installed) whatever drying system the customer wants, providing it will fit on the press,” he says. “The purpose behind an Aquaflex drying system is to give the customer another choice—one that we know will deliver all the capabilities and flexibility that has been designed into the press.”
When Aquaflex designs its presses, it designs them to address not only the current, but also the emerging needs of printers. “Our design objectives are to build in the most operational flexibility possible. Often, we find the dryer package can be a limiting factor,” comments Rosenbaum.
Rosenbaum cites the following example: you can run most applications with a standard IR dryer, however, when running a shrink sleeve application, IR drying can melt the thin shrink film unless you have just the right amount of forced air. “That’s what we do with our Aquaflex water-based dryer,” he says.
Aquaflex uses adjustable recalculating forced air and combines IR bulbs when needed for a high-efficiency solution. This closed-loop system does not require an external ductwork system for venting. When additional heat is needed, additional IR bulbs can be easily added. “We believe our dryer option adds greater flexibility and control over the drying process, and that will enable the printer to produce a wider variety of jobs,” says Rosenbaum.
In the end, the choice is up to the converter. According to Rosenbaum, some printers are more comfortable using dryer systems they are familiar with. “They know how their jobs will run, and there is little or no learning curve involved,” he says. Rosenbaum adds that the choice to buy an Aquaflex dryer package on a new Aquaflex press is often tied into why the purchaser is buying the new press in the first place. Often it is to provide new capabilities such as flexible packaging or better reproduction at higher speeds. “Having your press manufacturer assume the responsibility for making everything work in harmony can make the transition much easier.
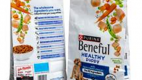




