Calm, Cool Converting
With a name originally inspired by the Puerto Rican beach resort town of Palmas del Mar (which in English means "sea palms"), Palmas Printing offers its customers an oasis of sorts from the ever-changing demands of the packaging marketplace. Case in point: cigar companies, Palmas' primary customer segment, have counted on Palmas to continuously—and with seamless calm—re-strategize and retool its printing and converting capabilities, as cigar packaging has effectively transformed from labeling to flexible packaging configurations. Jim Love, vice president, confirms that Palmas "has morphed repeatedly to stay capable of what our clients want and what the environment we operate in requires."
Printing, converting, and finishing firm George Schmitt & Co. (based in Guilford, Conn.), a family-owned company led by third-generation owner Robert Gunther, founded Palmas in 1974 in order to serve the cigar band business via a separate Puerto Rico-based gravure unit in close proximity to primary tobacco clients. According to Love, Palmas has remained a primary supplier to the cigar industry because of the specialized capabilities it has honed for this small market segment, including multiple print processes (everything over the years from gravure and letterpress to rotary screen, hot stamping, and flexo), nested printing designs, and roll re-registration diecutting for roll form cigar bands. Still under the ownership of the Gunther family, Palmas enjoys an underlying stability that facilitates its nimble reactions to customers' fluctuating market needs. Love explains that George Schmitt & Co.'s history sets a strong corporate tone for reinvention: Schmitt began as a lithographic company in 1874 and today is a multiple-location, multiple-process printing, finishing, and converting services firm. "Palmas inherited this ability to regularly re-invent itself and stay viable," he observes.
In the past ten years alone, Palmas has navigated an impressive succession of major operational changes, all designed to more effectively serve present and future customers. In 2006, the company transitioned its production capabilities from Juncos, Puerto Rico to Melbourne, Fla. in order to consolidate its facility within a larger, 30,000-sq.-ft. plant environment. Concurrent with the production move, Palmas discontinued all gravure and letterpress printing in favor of flexo printing. Says Love, "In recent years the quality of flexo has improved dramatically, challenging gravure and letterpress, which are both more expensive and slower to make ready and run on ever smaller and varied orders." He adds, "Our focus has been on higher volume applications and we chose to concentrate on flexo some years ago. We see our water-based and UV flexo capabilities carrying us well into the future."
With the move to Melbourne complete, Palmas was prepared with bolstered operational space and resources when, a few years later, cigar packaging underwent several rapid configuration changes. In 2009, when cigar manufacturers required laminated metallized film wrappers in place of the cigar bands that Palmas had produced for decades, Palmas opted to invest in new servo-driven flexo film presses and finishing equipment in order to produce the wrappers. Just two years later, Palmas was faced with cigar firms' unexpected migration from film wrappers into multi-wall zipper film pouches, and again moved quickly—this time to acquire multiple reciprocating pouch forming machines.
Organizing around flexo, flex pack
Today, Palmas' operation includes four flexo presses with capabilities ranging from 10˝, 6-color printing to 16˝, 10-color printing. Key features of these presses include water-based and UV printing stations, cold foiling capability, inline diecutting and slitting, and roll-to-sheet production. According to Love, the company will continue a strong focus on narrow-web production, but will not close the door on the prospect of wider press configurations in the future. "As Palmas and its customer base grow we are willing to move into other arenas to help meet the market needs," he states.
The company's converting and finishing services encompass slitting, inspecting, rewinding, diecutting, laminating, and pouch forming. Notable equipment additions at Palmas in the past 12 months have included its third film doctoring/slitting machine, two zipper pouch-forming machines and a solventless laminator—all, says Love, intended to support anticipated growth in flexible packaging volume. In the next year Love expects that Palmas will make further preparations for increased flexible packaging production with the purchase of one to two additional pouch-forming machines, as well as shrink film seaming and cutting machines.
Palmas complements its printing and converting operations with related services including in-house prepress, laser engraving, and digital platemaking. A particularly impactful investment, says Love, was the addition of a CTP unit. "As artists continue to design more complex and challenging graphics with gradients and screens, the CTP unit allows us to meet or exceed the quality of gravure and letterpress," he relates.
An open-door policy for growth
As a more recent entrant to the flexible packaging arena, Palmas has gained a number of fresh avenues for growth. Love says cigars and related tobacco industry products should remain Palmas' primary client base, but the company has its eye on new business opportunities in film pouches, particularly in the food and beverage category. Other promising segments, he notes, include miscellaneous pressure-sensitive labels for pharmaceutical, nutraceutical and personal care products, and shrink sleeves. A key entry strategy for Palmas will be the targeting of local and regional brands that may not be of interest to larger wide-web flex-pack converters. Overall, Love says Palmas sees "flexible packaging as a new area away from the excess capacity that exists in narrow-web label printing today."
A beneficial by-product of Palmas' transition to flexible packaging production is a strengthened problem-solving partnership with clients. "Unlike label printing, the category of flexible package printing can involve a greater variety of materials that can be combined for appearance, functional barrier, or even new packaging formats to replace labeled and printed boxes, cans, bags, and bottles, while reducing cost and increasing consumer appeal," Love states. "This requires more research and testing to offer the optimal construction for a variety of products."
Palmas experienced this positive dynamic firsthand when it moved into film cigar wrapper production. "We tested and offered a variety of metallized films with high-barrier properties allowing the client to market additional shelf-life and prolonged freshness," Love recalls. "Ultimately, this led to the next-generation pouch format, which has greatly improved shelf-life as a result of full-perimeter sealing without any gaps."
Love emphasizes that Palmas' operations are best suited for "large-volume, long-term opportunities that could become the next or additional focus for the business." And for a printer accustomed to regular reinvention, those opportunities could be in areas far afield of cigars or flexible packaging. According to Love, one "notable additional focus" that is on the horizon for Palmas is RFID tags, labels, and security print, because it is an active application area for parent company George Schmitt, particularly in the airline and pharmaceutical segments. "In support we have upgraded our facilities, procedures, and equipment to complement [George Schmitt] and qualify as a backup," Love explains. "This means that a full range of RFID placement and inspection equipment resides in our plant and is available to us for any new business we might attract on our own."
Such well-defined visions and preparations for the future should enable Palmas Printing to smoothly adapt to the future waves of significant change in the label and flexible packaging marketplace. pP
- People:
- George Schmitt
- Jim Love

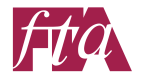
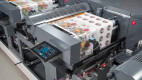

