It's a Smorgasbord
Today's narrow-web presses provide a wide range of options for highly flexible and productive package printing.
PRINTERS IN THE narrow-web, product-decoration business are asking—and being asked—to do more and more for their customers at virtually every turn. Competition is fierce at all levels of the supply chain and successful companies are doing everything they can to protect their existing business, while expanding into growth areas. Many times, these efforts require new technologies and capabilities.
Manufacturers of narrow-web printing presses are responding to the needs of their customers by providing a sophisticated array of features on their press offerings. The results of these efforts can be seen in the incredibly flexible and productive machines that are available today.
One of the overriding industry trends cited by Jon Guy, president of Gallus, Inc., is the elimination of the "'human error factor' from the printing equation. [It] is the removal of variables to production—automating to eliminate human error through a digital workflow process, which builds consistency and repeatability."
What this is leading to, says Guy, is the eventual integration of the press into a digital workflow. "The major benefit that a completely digital workflow provides is it enables printers to complete a job with consistency when the brand owner requires them to break up the job into smaller runs instead of one big run."
The need to improve workflow and profitability for its customers led Aquaflex to introduce Lean Manufacturing Principles in 2000. "We have seen this concept take root and prove its value," says Mac Rosenbaum, vice president of Aquaflex/F.L. Smithe Machine Company, Inc. "Today printers are acutely aware that workflows and process improvements have a direct impact on their bottom line."
Rosenbaum reports that the Aquaflex ICT® Instaprep press was specifically designed to be "lean friendly." "By enabling off-line job set up and clean up, our patented ICT system helps printers get more productive hours out of their press—that means a faster ROI and a better bottom line," he says.
Press flexibility is a requirement that Harold Jacob, product manager for Gallus, says is being driven by the ever-increasing expectations of brand managers, coupled with decreasing converter margins. This drives a "greater demand for flexible technology that provides both combination, value-added printing and higher efficiencies on a press."
One important key to maximizing a converter's investment is the ability of a press to handle a wider range of substrates. Jacobs sees a move toward thinner substrates as both converters and consumer product companies strive to take advantage of the cost savings they can offer. "The caveat is that you need a press with advanced technologies to handle the more delicate substrates," he cautions.
According to Rosenbaum, the increasing demand for flexible packaging is having an obvious impact on the narrow-web printing industry. "We find that traditional label printers are looking to flexible packaging for diversification. Commercial printers are also looking at package and flexible printing opportunities to offset the flat or declining market growth in commercial printing. Key to both of these trends is web width, and the ability to print on a wide range of substrates."
Aquaflex's newest press, the FPC, is a multiple substrate servo press that is targeted for cartons and flexible packaging. It is designed for high-quality printing on widths from 20˝ to 32˝ and at speeds up to 1000 fpm, says Rosenbaum. It features sleeve technology for both the print cylinder and anilox rolls.
When asked what press technologies narrow-web printers should consider, the answers were fairly general, reflecting the need to match any number of technologies to the particular plans of a printer. However, Mike Schmidt, VP of sales for Nilpeter USA, listed three specific areas: combination printing, printing on unsupported films, and in-line or off-line production of RFID labels and antennae.
The use of combination printing is one result of a trend toward consolidation, where larger converters are buying mid-size companies. "These larger companies then need to 'raise the bar' in terms of quality and service," said Schmidt. "These companies are looking at combination printing, including offset, screen, and UV flexo."
Companies such as these can look to Nilpeter's offset-based MO-3300 printing platform. It offers any combination of offset, flexo, screen, gravure, and hot and cold foil stamping.
Codimag, a company that specializes in semi-rotary label presses, offers its VIVA line as a letterpress and as a waterless offset machine. Its VIVA 340 press can also provide in-line combination processes including hot foil stamping, UV flexo, rotary diecutting, screen printing, embossing, and laminating.
The semi-rotary screen printing station was developed in partnership with Stork. According to Codimag CEO Alain Demol, "Screen printing is increasingly important for label printers everywhere in the world who want to expand into areas like cosmetics and body-care labels."
Ko-Pack's Model 400 15˝ Combination Press incorporates a modular design to allow UV flexo, UV rotary screen, UV letterpress, UV waterless offset, and rotary diecutting options. In addition, optional add-on units can provide in-line reverse printing, wet and dry laminating, hot stamping, and sheeting.
Super servo
The use of servo drives in new press designs is an example of one technology that has taken a firm hold in the industry. Servo drives can provide the flexibility, automation, and reliability that result in faster makereadies, higher uptimes, less waste, and the ability to run a broader array of jobs on a single press.
Gallus can point to its modular RCS 330 press as an example of a servo-driven press that offers many productivity advantages. In addition to process combinations that include UV flexo, rotary screen, hot foil stamping, and rotary diecutting, the servo technology allows the changeover of repeat jobs on the fly. This is accomplished by setting up unused stations while the press is running.
Edale offers servo drive technology on its Sigma line of narrow-web flexo presses. These presses are equipped with servos on each driven axis and can also be provided with independently servo-driven printing rolls that provide infinitely variable repeat length from 10˝ to 24˝.
The Sigma can run a wide range of substrates from unsupported films to paperboard. The key to this capability, especially with thinner films, comes from the ability to maintain constant web tension throughout its speed range.
Mark Andy launched its XP5000 servo-driven press line at Labelexpo last year. According to Ken Daming, director of product management, the press includes state-of-the-art servo-driven print and diecut stations, with full electronic register control and job handling. Mark Andy also offers remote diagnostics over the Internet to further maximize productivity.
The XP5000 uses Mark Andy's modular Multi-Process Productivity Platform that features the fully interchangeable QC (Quick Change) cassette system. Daming says eight different printing and finishing processes can be used, including rotary screen, hot foil, inter-station die, cold foil, and inkjet.
Omet's VaryFlex press line can run pressure-sensitive labels, flexible packaging, and folding cartons. It is a servo-driven sleeve press, with servo control of the plate carriers, impression rollers, anilox rollers, pan rollers, and chill drums.
PCMC has incorporated servo drives in its Evolution™ Flexo Presses. These presses are available with print widths of 18˝, 22˝, and 26˝, with infinitely variable repeats ranging from 9˝ to 24˝. They also feature job recipe recall and the ability to run substrates ranging from 0.5 mil films to 18 pt. board.
by Tom Polischuk
Editor-in-Chief
- People:
- Mac Rosenbaum





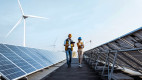