The Dish on Dots
Most screening technologies work well. Every prepress workflow presents a multitude of screening options. Beyond these simple assumptions, however, questions proliferate. Is AM screening the right choice, or is FM better? Will transitional screening supplant them both? What are the tradeoffs? How tight a process control window can the printer operate within?
The answers to these questions vary from market to market and from one print discipline to another. What is certain is that the right choice of screening method can help printers in their quest for differentiation. It can also have an impact in the pressroom, based on its runnability.
Screening has a long history. Developed long before the advent of digital imaging technologies, conventional Amplitude Modulation (AM) screening places halftone dots in a consistent pattern, varying the size of the individual dots to simulate the tone values of the original. It has proven to be very stable and to produce the most realistic flesh tones.
Frequency Modulated (FM or stochastic) screening randomly places dots of the same size, in different concentrations, to reproduce continuous tone. With the FM method, it is possible to produce very fine detailed print, highlight, and shadow areas, and eliminate the moiré and broken lines associated with AM screening.
More recently, screening technologies designed to compensate for the deficiencies of each method combine the best features of AM and FM screens. These so-called “transitional” screens are said to be easier to print, due to the need for less rigorous process control.
In sorting through the extensive array of screening options available to today’s package printer, we spoke with Steve Musselman, senior manager for the market development of digital solutions and emerging technologies, North America, Agfa; Mark Sanworth, vice president of technology, Artwork Systems; Tyler A. Harrell, flexo implementation quality manager, Esko-Graphics; Bryan Hughes, product manager, elecronic products, Enovation Graphic Systems, Inc.; Mark Tonkovich, product manager, CtP and proofing, Heidelberg USA; and Gordon Pritchard, Value in Print marketing manager, Kodak (Canada). Subject matter experts Socrates Rettos and Gary Russell of Phototype spoke about the company’s proprietary screening technology (see sidebar).
pP: FM screening has been around for more than a decade. What is driving its adoption?
AGFA: With the recent introduction of XM screening technologies from Heidelberg and Harlequin to complement Agfa’s :Sublima XM, along with Esko’s Samba and Kodak’s MaxTone, the writing is on the wall for the future of FM. FM has proven to be difficult to work with in prepress and onpress, with little onpress color adjustment possible, and debate rages on as to whether FM truly offers the benefits it has touted over the years.
ARTWORK SYSTEMS: Four factors: screen visibility, image detail, press stability, and color saturation. Low spot size FM screens are less visible than medium ruling AM screens and carry greater image detail. Because small spot sizes carry a limited ink thickness, they offer greater press stability. A 20µ FM spot will carry only about a 2µ thick film of ink. Even as more ink is applied to the plate, the 20µ spot will not accept it. The result is more stable printing. Thinner ink films also produce greater color saturation. The obstacle to FM screening is a grainy appearance.
ESKO-GRAPHICS: FM screening typically does not produce terrific results from highlights, through midtones, to shadows without a lot of work. The biggest drawback to FM screening is high midtone gain. FM screening typically is used for highlights and shadows. Just like any screening technology, it depends upon how well that technology suits the kind of work you are doing—how fine the work is, and what kind of substrate you are printing on. The rest is how adaptable your press, substrates, and process are to FM screening.
FUJI/ENOVATION: Print buyers want a reproduction as close to continuous tone as possible. The relatively low adoption rate of FM screening is due to the tighter process tolerances required to be successful. The majority of printers who implement alternative screening technologies do so because a client has requested or specified it. Subject matter moiré with certain print jobs also drives the printer and print buyer to consider these technologies.
HEIDELBERG: Heidelberg’s first FM screening technology, Diamond Screening, was launched in 1993. Our second generation Satin Screening was introduced in 2004. In 2006 we have further optimized this screening with our newest screening Prinect Hybrid Screening.
In 1993 computer-to-plate (CtP) was not widely accepted. As a result, many of the advantages of FM screening were overshadowed by problems in the film-based workflow. It was difficult to contract-proof and calibrate. Since the advent of CtP, all of the film-based problems associated with FM screening are eliminated. FM screening offers a stable print run, moiré-free printing, smooth reproduction of vignettes, and sharp details. A key requirement is very good process control in the prepress area and on the press.
KODAK: FM screening entered the digital domain in the early 1970s as a method for rendering tones on the bi-level (green/black) computer displays of the day, since they did not have the resolution to build small-enough conventional AM halftone dots. Offset printing presses are somewhat analogous, since they are essentially binary in nature. Like any other halftone screening technology, FM screening compensates for the inability of the press to reproduce the continuous tones of the original art. What drives the further adoption of FM screening in offset is the printer’s desire to meet customer expectations, lower manufacturing costs, and differentiate themselves from their competition.
pP: What is meant by so-called transitional screening and what is driving its development? That is, how does transitional screening address the problems with conventional and stochastic screening?
GFA: Not all transitional screening solutions are created equal. The problem with many transitional screens is the visible crossover where FM and AM meet. The challenge became how to combine the two technologies seamlessly, without noticeable intersections.
XM (or cross modulation) screening provided the solution. Agfa’s :Sublima XM technology applies a common sense approach to advanced screening: match the screening to the pressroom environment, rather than changing the pressroom to match the screening requirements. XM screens take into consideration the type of paper typically used, such as coated, uncoated, or recycled; the printing architecture, such as flexography; and other variables. XM screening works within the established parameters and uses the smallest optimized and printable dot for the application. Since XM screening algorithms combine the best of both the AM world and the FM world, the matter of “best fit” depends on stock characteristics and how much flexibility one desires on press.
ARTWORK SYSTEMS: Hybrid Screening is a trademark of Artwork Systems, Inc. A Hybrid screen contains FM and AM screening within a single image (typically, FM in the highlight and AM through the rest of the scale). These screens are commonly used in flexo to achieve white highlights under conditions of extreme highlight dot gain. Their value in offset is limited.
There is another screen that is referred to as a “hybrid” but is really an FM screen with a less random pattern than a typical first or second order stochastic screen. These screens feature a “speckle” shaped dot instead of a pure circle or other geometric pattern. Because they have a less random distribution of dots, they appear smoother then many FM screens—particularly under less than perfect printing conditions. However, they are not as smooth as AM screens and don’t have the color saturation or press stability of true stochastic screens. Hence, while their benefits are real, they actually represent a compromise between FM and AM screens. The ideal screen would not be a compromise between AM and FM screens, but would offer the best of both screens: the smoothness of AM with the press stability and color saturation of FM.
ESKO-GRAPHICS: Transitional screening refers to the mixing of AM and FM screens within a tonal range. Transitional screening uses FM in the highlights and shadows, AM in the midtones, and has been shown to yield a printable line screen. In the midtones, AM screening is preferred because it generates less dot gain and a clean tint. However, in the highlights and shadows, where the dots become too small for easy reproduction, the AM screen transitions to a FM. These screens have shown particularly good benefits in flexo printing, but also are being used for offset.
FUJI/ENOVATION: The whole idea behind transitional screening is to improve the printability of FM. Transitional screens typically start with stochastic in the highlight areas, transition to AM in the midtones, and transition back to stochastic in shadow areas. The goal is to provide easier printability in the midtones and better detail in the highlight and shadows.
HEIDELBERG: It is possible to print high line screens with AM screening. The downside is the higher the screen ruling, the finer the highlight and shadow dots become. Eventually, they reach a point where they are too small to print.
Transitional screening solves this problem by maintaining a minimum dot size, but reducing the number of dots needed to achieve to proper tonal value. In this way the lightest and darkest of tones can be reproduced more accurately, avoiding harsh breaks in the highlights and “plugging” in the shadows. Transitional screening is easier to print than stochastic and requires less stringent process controls.
KODAK: Transitional screens capture the benefits of AM and FM screening while avoiding their deficiencies. Typically, hybrid screens are classed according to which screening method forms the largest proportion of the tone scale. A transitional AM screen, also known as a “cross-modulated” or XM screen, is primarily an AM screen with elements of FM. A transitional FM screen is primarily an FM screen with elements of AM.
Transitional AM/XM screens are useful primarily in flexographic applications, where the RIP, imaging device, plate, or print reproduction process cannot render dots smaller than a given size. Transitional FM screens use larger midtone dots that are less affected by imaging variations, are easier to resolve, and generally produce smoother tone renderings in flat tint areas than first order FM screens.
pP: Why might a printer choose finer line rule AM screening over FM or transitional techniques?
AGFA: AM screens vary the size of the dot on an established grid or line-screen ruling to change the tonal value. The finer the grid, the higher the frequency or number of dots and the closer the rows of dots are to each other. Varying conditions of the prepress process and the types of presses being used limit the screen ruling. The printing process, therefore, determines the choice of a traditional AM screen ruling; it is not solely a decision of preference.
ARTWORK SYSTEMS: AM screens produce smoother results than FM screens. This is because uniform patterns (AM) appear smoother to the eye than random patterns (FM). At screens below 200 lpi, the human eye can actually see the dots as well as the overprint patterns formed when multiple AM screens are printed on top of one another. AM screens greater than 200 lpi have the potential for high-quality results. However, the higher the screen ruling, the more difficult conventional AM can be on press. Even at 250 lpi, a 50 percent dot is about 80µ in diameter and will carry about an 8u film of ink. Such screens have excessive dot gain, poor stability, and do not have the color saturation of FM screens.
ESKO-GRAPHICS: The AM grid works well as a visual concept. In certain areas, the grid pattern of dots in AM screening is much better than in FM. For example, FM screening rarely looks good on flesh tones and should be used only for highlights and shadows.
FUJI/ENOVATION: It’s a dot structure printers are comfortable with. If their processes can hold higher screen rulings, dot gain curves can be adjusted, and they could see an immediate impact on the quality of the piece without purchasing additional screening technology. Again, it’s all about the process! Higher screen rulings also narrow the process control window.
HEIDELBERG: The main advantage is that it is easier to make plates and easier to print.
KODAK: A finer AM screen could be an alternative in situations where an FM screen is not appropriate; for example, in gravure and flexographic printing.
pP: Would you elaborate on the function of process control in AM, FM, and transitional screening?
ARTWORK SYSTEMS: With each screening technology, there are three basic steps to process control: selection of screening attributes, press characterization, and a monitored press run to assure actual results match desired results. Step one differs because the attributes of each screens differ. For an FM screen, the attribute to determine is the spot size (e.g. 10µ, 20µ, 30µ, etc.). For AM screens, the attribute to determine is the screen ruling. Press characterization and process control are the same for all screening technologies. For Artwork Systems’ Concentric, the attributes to determine are screen ruling, ring width, and space width. Like FM spot sizes, ring width and space width are expressed in microns.
ESKO-GRAPHICS: In AM screening, moirés can also occur when patterns in objects or backgrounds conflict with the line screens in use. Textiles, for example, can interfere with a printed screen. CtP increased the popularity of FM screening because CtP produces a first-generation dot, rather than one created first on film, then burned onto the plate. Because there are no line screens or screen angles in FM screening, images are reproduced without rosettes, and the result is moiré-free images, sharper dots, improved registration, and greater consistency overall.
Another characteristic of FM screening was color stability in the pressroom. However, it was difficult to make color adjustment on press, even to the point where new plates had to be made. And, since different substrates had different characteristics, curves for individual stocks were also sometimes needed. Because FM should only be used for highlights and shadows, most transitional technologies use AM screening in the midtones, and some sort of FM or other pattern in the highlights and shadows. Transitional screening takes the best screening option at every point in the tonal range and for the particular substrate and application, to achieve the best results by providing new screening patterns or transitions between AM and FM screens.
HEIDELBERG: CtP devices and the resolution of the plate need to meet the needs of the final printed product. In all applications, dot gain has to be determined and programmed based upon paper stock, ink, and screening technology to meet the target specification. Process control ensures that what is in the digital file will be accurately reproduced in the proof and on the final printed sheet.
KODAK: Process control is a basic requirement of cost-effective print manufacturing. As halftone screens become finer and finer, process control will become even more important. That being said, most of the dot sizes typically used in second-order FM screens (20-25 microns) do not require any more process control in printing than equivalent AM or hybrid AM/XM screens (175-240 lpi).
pP: For what applications and under what conditions would conventional, stochastic, or hybrid screening be an appropriate choice for a package printer?
AGFA: Flat tints, process-build brand colors, etc. are a perfect fit for XM screening, as FM screens tend to be grainy with flat tints. The regular orthogonal AM grid of XM screens gives a smoother appearance than grainy FM.
ARTWORK SYSTEMS: We used to have a complex decision tree to help decide between AM and stochastic. The more we learn about our Concentric Screening, the more it appears to be a logical choice for all offset printers. One thing we have learned about Concentric is that high ruling concentric screens require high-quality plate materials and a properly adjusted CtP unit. If you can’t image quality 20u stochastic screens, you won’t be able to image high-ruling (above 200 lpi) Concentric Screens with thin rings (below 16 microns). Such screens will show patterning on both plate and press. However, we have recently had a few printers lower screens (to around 180 lpi), increase ring widths (to 20 µ), and achieve results superior to conventional AM.
ESKO-GRAPHICS: Conventional AM screening is better for tints and flesh tones. FM screening is best for printing detail as well as in highlights and shadows. It can also be helpful in areas where a number of printed colors and tints could create a moiré. Transitional technologies try to resolve certain deficiencies in both, such as generating even better highlights and shadows, or providing transitions during the midtones.
FUJI/ENOVATION: We are beginning to see more implementations in this market. If printers want to use four-plus colors, stochastic is appropriate. We are seeing an interest in the flexo market in using multiple screening technologies on the same page or package. The reason for this is that tone dot gains are much higher in flexo than in commercial offset. By combining screening technologies, flexographers can balance the job better than just hitting one particular element and letting the rest fall where it may.
HEIDELBERG: Prinect AM Screening is applicable in any high-quality printing. In particular, Heidelberg Irrational Screening provides true conventional angles and its accuracy greatly reduces the potential for moiré compared to Supercell AM screening. Prinect Hybrid Screening allows the printer to produce very high screen rulings while maintaining the highlights and shadows. If color needs to be manipulated on press, both respond to density moves. Prinect Stochastic Screening is a perfect fit for greater then four-color process work. Without angles, screening moirés are eliminated and angle selection is unnecessary. It is a very stable process.
KODAK: Transitional AM screening is best for flexo packaging applications since it allows for the recovery of much of the tonal scale that would otherwise have been lost due to the lack of resolution of flexo plates. For metal offset printing, transitional AM/XM screens allow higher screen frequencies on lower resolution plate imaging systems. They do this at the expense of highlight detail and smoothness and offer no advantage in the pressroom over equivalent AM screens. Transitional FM screens can be used on all packaging substrates and eliminate the issues of first-order FM screens while preserving many of their lithographic advantages.
pP: How do you differentiate your screening products from others on the market?
AGFA: As a unique solution to an age-old problem—how to maximize the quality of my print—Agfa encourages its customers to position themselves smartly when it comes to :Sublima. While many printers too often fall into the trap of offering bargain-basement prices for their high-quality work, we encourage our customers to put a premium on their :Sublima-powered print.
Agfa recently launched the inaugural “:Sublima Distinctive Marketing Awards” for printers who go out of their way to promote themselves and the great work they do, courtesy of :Sublima. It is critical for those who use :Sublima to make sure their market knows that it is no accident that they are providing high-quality print that few others can match.
ARTWORK SYSTEMS: Our Hybrid Screens are for flexo. We don’t promote them in the offset world, where benefits are tenuous, at best. It is true that a little bit of “stochastic” or “dot deletion” in the highlight of high ruling AM screens can help preserve grey levels. We’ve built this into our Paragon and Concentric screens at no additional charge. Our second order stochastic Organic Screening has been shown to produce superior results on press. Concentric is the easiest screening to differentiate from other technologies in the market: it’s the world’s first and only non-solid halftone dot. Concentric screens are AM screens, but instead of the traditional solid halftone dot, the Concentric screen is divided into rings. The color saturation and press latitude of 20 µ stochastic can be achieved using Concentric Screens with dots divided into 20 µ rings. Printers can achieve screen rulings 1.5x to 2x their current screen ruling.
ESKO-GRAPHICS: All of Esko’s screens are variations of AM, FM, and transitional options. Our latest screening technology, PerfectHighlights, helps to print, for example, corrugated boards, where soft polymer plates with high relief depths are used. In such cases, stray highlight dots are not sturdy enough to remain stable over a flexo press run. PerfectHighlights ensures that these dots remain printable and, thus, provides flexo trade shops and corrugated converters a visible way to differentiate their print quality from competitors.
Esko also differentiates itself with Screen Manager, a component of our Scope workflow suite. Laying down ink on different substrates, such as high-quality, high-gloss paper, corrugated, or a difficult flexible substrate produces different results. Screen Manager allows you to build your own screening with a mixture of screening technologies in any part of the tonal range. For example, you could decide to create a screen with stochastic technologies to 8 percent, 10 percent or 12 percent highlight tones, select a round or elliptical screen for the midtones, and our Groovy screens for the shadows. It’s personalized, job-specific screening.
FUJI/ENOVATION: Fuji’s screening technology was developed by scientists in Tokyo working with Enovation plates and engines. We all know the more “noise” that is removed from a screening algorithm, the more difficult it is to print. The human eye perceives or is more sensitive to certain things. Memory colors, such as green grass or blue sky, are weighted as more important in the “math” of the solution. Screening is no different. If we keep some of the noise but move it to areas that are less perceptible to the human eye, we maintain a higher degree of printability. Printability is key. Printers spend huge amounts of human and capital resources, trying to achieve it. We are very sensitive about providing them with products that improve their processes without narrowing their control window to a point where they produce fewer jobs per day. This is why our Co-Res (transitional screening) was developed and released before our Taffeta (FM screening) product.
HEIDELBERG: Heidelberg’s screening transition goes back to the invention of electronic screening by Dr. Hell and continues with the Heidelberg Prinect Screening Family. Prinect AM Screening is standard with Heidelberg RIPs and with our patented Irrational Screening. Prinect Hybrid Screening provides the user with higher line screens and detailed control of the end points, yielding high-quality, photorealistic output. Prinect Stochastic Screening is the newest generation of second order stochastic on the market.
KODAK: While Kodak Staccato, Kodak MaxTone, and Kodak Hyperflex are all award-winning technologies, it takes more than a specification to differentiate a product. With screening, that involves at least four elements, whether the screening is FM, AM, or transitional AM/XM/FM: the design of the screens (distribution, pattern, and shape of the dots); the quality of the plates or film/plate combinations; the plate exposing technology; and customer training and service support infrastructure.

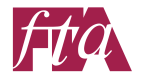
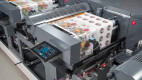

