The Dish on Dots
pP: Would you elaborate on the function of process control in AM, FM, and transitional screening?
ARTWORK SYSTEMS: With each screening technology, there are three basic steps to process control: selection of screening attributes, press characterization, and a monitored press run to assure actual results match desired results. Step one differs because the attributes of each screens differ. For an FM screen, the attribute to determine is the spot size (e.g. 10µ, 20µ, 30µ, etc.). For AM screens, the attribute to determine is the screen ruling. Press characterization and process control are the same for all screening technologies. For Artwork Systems’ Concentric, the attributes to determine are screen ruling, ring width, and space width. Like FM spot sizes, ring width and space width are expressed in microns.
ESKO-GRAPHICS: In AM screening, moirés can also occur when patterns in objects or backgrounds conflict with the line screens in use. Textiles, for example, can interfere with a printed screen. CtP increased the popularity of FM screening because CtP produces a first-generation dot, rather than one created first on film, then burned onto the plate. Because there are no line screens or screen angles in FM screening, images are reproduced without rosettes, and the result is moiré-free images, sharper dots, improved registration, and greater consistency overall.
Another characteristic of FM screening was color stability in the pressroom. However, it was difficult to make color adjustment on press, even to the point where new plates had to be made. And, since different substrates had different characteristics, curves for individual stocks were also sometimes needed. Because FM should only be used for highlights and shadows, most transitional technologies use AM screening in the midtones, and some sort of FM or other pattern in the highlights and shadows. Transitional screening takes the best screening option at every point in the tonal range and for the particular substrate and application, to achieve the best results by providing new screening patterns or transitions between AM and FM screens.
HEIDELBERG: CtP devices and the resolution of the plate need to meet the needs of the final printed product. In all applications, dot gain has to be determined and programmed based upon paper stock, ink, and screening technology to meet the target specification. Process control ensures that what is in the digital file will be accurately reproduced in the proof and on the final printed sheet.
KODAK: Process control is a basic requirement of cost-effective print manufacturing. As halftone screens become finer and finer, process control will become even more important. That being said, most of the dot sizes typically used in second-order FM screens (20-25 microns) do not require any more process control in printing than equivalent AM or hybrid AM/XM screens (175-240 lpi).

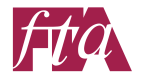
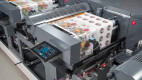

