CTP Flexo: A Bright Idea
Necessity is the mother of invention.” Plato gets credit for coining this phrase. While this is unquestionably true, it’s the forces of “necessity” that are relative. For example, necessity reared its head somewhat earlier in the offset world than in the world of flexographic package printing, where the migration from analog (film-based) to digital platemaking still lags the adoption of computer-to-plate (CTP) in other segments of the industry.
There are signs that this is poised to change. As consumer product companies and big box retailers look to drive sales through innovative, high-quality packaging—delivered faster and at lower cost than ever before—their printing providers are investing in flexo CTP to increase efficiency and cut waste. Despite estimates that only about 20 percent of packaging facilities worldwide currently use digital plate technology, the economic and creative advantages of CTP flexo are persuasive. Digital plates are said to promote better registration and dot reproduction, faster makereadies, more reliable process controls, and guaranteed repeatability that enables printers to react faster to customers’ needs.
CTP flexo: A primer
A flexographic digital plate consists of a photopolymer layer topped by a carbon-based masking layer. Flexographic CTP uses infrared lasers to ablate portions of the masking layer to uncover corresponding areas on the photopolymer layer.
Digital imaging of flexographic plates begins with placement of the plate material on an external drum or sleeve. As the imaging drum rotates, a laser head creates the image on the plate, creating a pattern of appropriately sized and spaced raised dots. This method, called “imaging in the round,” eliminates the distortion that can occur when, as in conventional flexographic platemaking, a flat plate is mounted to the printing cylinder after imaging. The process creates only minimal debris, which is removed by an extractor built into the system, followed by a water wash and a drying period.
Because CTP flexo eliminates film from the workflow, it also saves time, material, and labor incurred when working with and storing film negatives. Corrections can be made quickly and cleanly to the digital file, as opposed to producing new films for imaging. Finally, digital platemaking can eliminate the need to deal with unpleasant byproducts of computer-to-film (CTF).
According to Ian Hole, director, marketing development, Esko-Graphics, “There is little difference between preparing a final file for computer-to-film analog plate production and preparing one for processing via CTP flexo. While the settings will be different, you still have trapping, color, step-and-repeat, and other issues to consider. The need to image smaller dots also means that you have to consider how to treat highlights and shadows. Most important, CTP flexo has to consider different dot gain curves, as well as the choice of a screening technology.”
Laura Ryan, U.S. and Canada regional marketing manager for Kodak’s Graphic Communications Group, Packaging Segment, points out that apart from curves, resolution, file formats, and production parameters, CTF and CTP workflows also will differ in “how the films and/or files are proofed before plating. In a CTF workflow, color keys or blue line proofs are produced to ensure the job is correct before plating. In a CTP workflow, the steps are the same, except that software applications are used to create a ‘virtual proof’ that is used to ensure the file is correct before imaging.”
Dot’s okay
In technical terms, the primary difference between a conventionally imaged flexographic plate and one that is imaged digitally comes down to the size of the dot. The dot on a conventional plate is larger than the dot on the negative and the top of the dot is flat.
In contrast, says Hole, “the shape of a digital dot has a better, stronger, conical top and gets a more precise transfer of ink relative to the size of the dot it prints.” Since the digitally imaged dot does not change size, the plate can hold a much smaller dot than a conventional plate, yielding a printed image that is closer to continuous tone quality than is possible with conventional plates. Because the exact size dot required on the printed substrate has already been produced on the digital plate, press impression is less critical to the size or sharpness of the dot print result, whereas in conventional flexo, fingerprinting of the proof to the press must take into account the higher dot gain.
Despite the benefits, the price of admission to the CTP flexo party is a major drawback to its more widespread adoption, according to Lenny Mizusaka, technical flexo division sales manager and Chris Van Duker, product manager, RIPit Corp. According to Mizusaka, “We think one of the major factors [for its sluggish uptake] has been the cost of CTP imaging devices. There’s a lot involved in the direct imaging of flexo material, and that has set the cost of entry pretty high.”
As a print discipline, however, flexography is generally less expensive than offset or gravure and, developments both on the scene and on the horizon, could prove persuasive to a larger segment of the flexo marketplace over time. “Costs on the equipment side are on their way down,” confirm Mizusaka and Van Duker. “We think that will encourage more users to make the jump. Another factor is the difference in cost between traditional flexo plate material and the kinds that work with digital imagers.” Recent thermal processing advances, such as Inline UV Main Exposure technology from Esko-Graphics, also could translate into a drop in the price of flexo plates.
A ‘capital’ idea
If a flexographer owns a digital-to-film workflow, and has an analog method for processing plates, the investment is in the digital imager, says Hole. Imagers cost up to $350,000, depending on the size and speed requirements, he adds. Payback for most imager investments is between nine and 24 months, depending on usage and plate volume, notes Hole.
Asserts Ryan, “Flexographers justify the investment in digital platemaking because their competition is investing in superior quality platemaking, and because their customers are requesting the improved quality print results made possible by digital flexo technology. Digital flexo brings improved consistency, stability, and repeatability to the platemaking process, which delivers benefits on-press and in the final printed label or package.” n
- Companies:
- GMG Americas

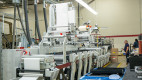



