In-Line Folding Carton Converting
In today's challenging business environment, folding carton manufacturers' profits are getting squeezed. Customers demand better quality, lower quantities, just-in-time (JIT) delivery, sustainability, and more point-of-sale "pop," all at a lower price. Yet, many converters are trying to meet today's challenges with yesterday's manufacturing processes, causing bottom-line profitability to suffer.
To make the situation more complicated, many end users see packaging as a commodity. In a commodity market converters need to follow time-tested business practices:
• Improve production processes—get lean and focus on driving costs out;
• Add value to your product—value innovate.
Printers that are still using the multi-step manufacturing technology from 10, 20, or 30 years ago will have a difficult time answering these production challenges. However, today's in-line flexographic production process provides folding carton converters the means to meet customers' demands and maintain profit margins. Flexo is no longer a secondary citizen of the printing world. Flexo press and prepress technologies have advanced so much in recent years that flexo printing can now be included among the best solutions.
Market demands
For many years, folding carton converters enjoyed long production runs with few product changes, and differentiation based on artistic talents. Those days are gone. Today, customers want smaller run sizes with more market-oriented changes (holiday, language, seasonal), delivered just-in-time to their plants. Quality and consistency are expected. Competitors are everywhere and supplier differentiation is becoming harder and harder. Price is an important factor that consumer product goods (CPGs) manufacturers use to separate suppliers.
For printers, the question becomes, 'How have your manufacturing processes adapted to meet these challenges?' If the answer still includes the use of older printing processes, company profits are probably being squeezed.
Car industry comparison
For comparison purposes, take a look at the auto industry and the changes in its production processes over the years. For years the Big 3 in Detroit used the Henry Ford assembly line production process and were very successful. They sold everything they built and made a handsome profit. Then the Japanese entered the U.S. marketplace with their Kaizen production philosophy and started to make inroads in the market. The once-invincible Big 3 thought no one would buy a foreign made car, but they were wrong.
The auto market had started to change—quality became demanded and expected, just-in-time production was required from suppliers and auto manufacturers. Product differentiation for all the car manufacturers became harder and harder, and price became a factor in the sales process. Now the Big-3 automakers use the Kaizen production concept, producing only what can be sold instead of flooding car dealers. They continually innovate to differentiate their products in the marketplace. In effect, they adapted their production processes to meet today's customer demands.
Lean and mean manufacturing
To remain profitable today, folding carton manufacturers need to look at their processes and make decisions on the best way to make money. The old argument that offset is better than flexo is no longer valid, and can lose its relevancy in a lean discussion. Offset presses have addressed current production challenges by going to bigger formats in recent years and have incorporated roll-to-sheet feeders, cold foil, and/or coating options to become in-line sheetfed solutions. The only problem is that the offset process can still require additional steps for hot foil, metallics, window patching, and diecutting that require additional personnel, additional storage space, and additional time. From a lean manufacturing perspective, being able to go from roll to finished diecut blank with fewer people, no added storage, less time, and less cost is the best solution. So why doesn't everyone have at least one flexo press in the production facility?
Years ago flexography was 'potato printing' compared to offset quality and that image had been hard to shake. It was almost like changing religions to go from offset to flexo. It required folding carton manufacturers to step out of their comfort zones for a process that did not answer all their production requirements. Advances in flexo press and prepress technology in the last few years have changed that dynamic.
Today's flexo presses bring more science (less art) to the production process. Completely servo-driven flexo presses eliminate all mechanical-related issues in the print process, eliminating gear-marking, for example. Job changes (color and copy) can be accomplished in less than 15 minutes on a 6-color press from good product to good product. Copy changes can be done on-the-fly, without the press stopping, generating very little waste. Job set up can be memorized and recalled for excellent repeatability and consistency. Print registration is completely automated and controlled, even throughout speed changes, to further enhance production consistency. In effect, the flexo press operator becomes like a press manager, since the press automation reduces the need for direct operator interaction.
The flexo process also enjoys some basic advantages. For example, it eliminates the need to balance water and ink, and produces a thicker ink laydown that delivers better color densities (more "pop"). Laser-engraved ceramic aniloxes provide consistent color from run to run. In addition, new on-press color management systems track and record color consistency for the entire production run, and flag or alarm the operator if there is a deviation. This enables flexo manufacturers to assure customers that they are delivering consistency throughout the production run and from run to run. In fact, the flexo printing process is much simpler from an operator point of view.
Value added
New in-line printing presses from suppliers such as Gallus can offer folding carton manufacturers increased flexibility. For example, the Gallus ICS 670 press is a completely modular platform. Every print station can easily be changed from HiDef flexo printing™ to screen printing, cold foiling, laminating, and even rotary hot foil embossing. Reverse printing can be done in any print station on the press. Additional print stations for rotogravure printing can be integrated.
With this flexibility, different print technologies can be combined in-line, on a press, to take advantage of the benefits of each technology—gravure for metallic, fluorescent, and specialty coating applications; rotary screen for tactile, texture, and Braille applications; cold foil for cost-efficient foil applications; and HiDef flexo printing for enhanced print quality and color density. Adding value to customers' projects can be achieved quickly and easily; a printer can 'value innovate' to differentiate its folding carton manufacturing capabilities from competitors.
As a further example of in-line production solutions, the Gallus FCL 670 flatbed system can provide roll-to-blank diecutting, similar to what folding carton manufacturers currently have, but integrated into the in-line process. Depending on production demands a rotary diecutting station can also be integrated.
But questions remain: can flexo match offset or gravure print quality standards, and how do I convert my files from offset to flexo?
Flexo printing
Just as flexo press technology has advanced in recent years, flexo prepress and plate technology has made dramatic advancements that have changed traditional thinking. For many years, offset and gravure argued over which had the best quality. Offset offered the ability to print high linescreens (up to 300 lpi) with soft vignettes (down to a one percent dot) with low-cost plates, while gravure offered excellent print quality with better color densities (more ink laydown), but with expensive print cylinder costs.
Today, thanks to developments such as Kodak's new FLEXCEL NX flexo plate system with DigiCap NX screening, flexo can now achieve up to 300 lpi with AM screening, and 20 micron FM screening; produce consistent dot sizes as low as a 10 micron dot; print all 256 gray levels down to a true 0.4 percent dot; and achieve the color densities similar to gravure, with plate costs that are much less than gravure. In addition, the Kodak FLEXCEL NX system can take existing offset or gravure files and use them to make flexo plates using AM or FM screening without additional prepress curves or separations.
Change is good
The folding carton market is changing, whether printers like it or not. This means, in order to survive and remain profitable, folding carton manufacturing processes need to change also. Modern flexo in-line production processes offer the production efficiencies, the quality, the "pop," and JIT benefits that customers demand. Combining the latest in in-line flexo press technology with the latest in flexo prepress technology can be the answer that folding carton manufacturers need. pP
Authors—This article was written by Steven Leibin, sales manager for Gallus Printing Machinery, in conjunction with Dr. John Anderson, director, packaging segment marketing, for Eastman Kodak Co.
(Editor's note: This article, written by Steven Leibin of Gallus Printing Machinery in conjunction with Dr. John Anderson of Kodak, highlights some recent developments in flexo process technologies.)
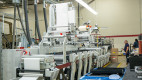




