Featured Products: UV, IR and LED Curing - January 2014
Lightouch Maximizer Combo UV/IR Dryer Ideal for Combination Printing
Combination printing requires a converter to utilize a variety of different ink chemistries to obtain the desired effect on the substrate for high-end printing requirements. In most cases this process involves the use of UV inks in combination with water-based inks printed in-line, in one pass. The Lightouch Versiflex UV curing system features a combination Maximizer IR drying system for a compact in-line solution that can be retrofitted into most converting lines. It incorporates a piggy-backed IR dryer with in-line UV, one small electronic control cabinet, and a shared exhaust system for both drying methods.
The system combines the sleek UV lamp cassette offered in AAA’s Lightouch UV line with the proven Maximizer Electric Impinged Air Infrared drying system in 4, 6, or 9 bulb configurations. Both systems allow operators to select UV or IR in each station for the desired ink system. Operators can also set a variety of variable features to optimize the dryer for the job at hand. Adjustable features include UV shutter timing for ideal web control and setting curing/drying intensity proportional to press speed at each station.
Both the UV and IR cassettes incorporate QC bulb features that promote good housekeeping due to a tool-less removal of the UV bulbs and IR emitters for routine maintenance. This compact in-line dryer can be a good fit for printers requiring flexibility in drying technologies along with fully adjustable performance.
For more information visit http://aaapress.com or call 847-818-1100.
LED: Coming soon to a dryer/curer near you
Drying and curing inks on packaging substrates has long been accomplished with mercury vapor technology that exposes the inks to IR and UV light. But over the next few years LEDs (light emitting diodes) will likely shoulder the older technology aside. LEDs are becoming commonplace in automotive and industrial applications and are available for household use. While expensive, LEDs boast significant reductions in energy usage and substantially longer lifespans than conventional lights, a long-term value that can make up for the added up-front cost. One company, AAA Press International will soon be rolling out a cost calculator to help you see how the savings could work in your operation. We’ll be taking a look as soon as it’s available and will report back here in packagePRINTING.
The LED light spectrum is fairly narrow, producing a single peak irradiance in the 385-390 nanometre range, which has limited its applications in the printing and converting markets. But LED technology has improved three-fold in recent years, offering higher power outputs and outstanding longevity. There have been barriers to entry in the flexographic printing and converting markets due to capital equipment costs, higher ink/coating costs and a lack of proven ink and coating suppliers. This is changing, clearing the way for a LED curing system to land on a shop floor near you.
LED Pros
- Up to 20,000 hour LED life versus 1,500 hours for conventional mercury lamp technology.
- 85% reduction in temperature at the web enables easier curing on heat sensitive films and papers eliminating the need for chill rollers.
- Energy consumption decreases up to 75% while yielding a 50% smaller carbon footprint.
- Maintenance costs can drop up to 85%.
- Solid State Electronics allow for instant on/off (no down time for warm ups) and infinitely variable power output for excellent heat management and significant energy savings.
- Compact, durable lamp heads for tight installations & easy integration.
- Compact solid state electronic power supplies reduce equipment footprint by 50%.
- Compact, efficient, low-energy, water cooling eliminates the consumption of ambient shop air to cool conventional lamps.
- Eliminates mercury lamps from your shop environment (mercury may well be banned in the coming years).
LED Cons
- Higher capital equipment costs of 2-3 times that of conventional mercury technology.
- Currently higher ink and coating costs.
- Presently only a few suppliers of inks, colors, and coatings (varnishes, adhesives, silicones, etc.) offers LED curable choices.
Thanks to AAA Press International for information on LED performance.
American-Made UV Roller Coaters with UV Curing Section
For the best source of UV it’s hard to beat the sun. But for a source you can use no matter the weather something a little more scalable is required. American Ultraviolet’s line of UV coaters begins with a small footprint, hand-fed roller coater designed for quick-copy and digital shops with limited floor space and ranges up to a fully automated forty-inch line available with all American-made feeders and stackers as options. AUV also offers large format roller coaters at 60 and 80 inches standard as well as custom coating and curing equipment. Standard features of AUV systems include:
- Easy removable applicator rollers for quick change over from UV to AQ
- Closed loop recirculating coating systems
- Adjustable coating head accepting up to 3/4-inch thick substrates
- 200 and 300 watts per inch power options
- Conveyor speeds from 40 FPM to 200 FPM
- Independent drive motors for conveyor and roller coater
- Air cooled with high efficiency blowers
- Dual purpose coating UV and Aqueous available
Contact American Ultraviolet at 1.800.288.9288 or online at http://americanultraviolet.com
EB: Taking a different approach
Unlike other curing methods, EB doesn’t deliver heat to the substrate. The chemistry being processed (inks, adhesives, coatings) changes from liquid to solid when cured with a curtain of electrons. Electron beam doesn’t use solvents, requires less power, and can lower overall costs, and reduce material waste. Food-safe and FDA compliant, EB has been used in primary food packaging for 40 years.
The latest electron beam offering from Energy Sciences is FlexoBeam, featuring web widths of 20 to 66 inches and speeds up to 1600 feet per minute. It handles EB inks, coatings and adhesives and can be installed to work with new or existing presses.
For more information contact: 978-694-9000 or http://ebeam.com





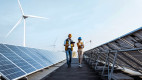