Dirty Static Problems
Contaminants and static create big problems for printers, but the right system will protect employees and increase production yields.
ANY PRINTER KNOWS there are several things that can ruin a job and harm the company's reputation. Dust, contaminants, and static electricity are just a few—but a costly few.
Static not only zaps press operators, but also attracts dust particles, hair, and other contaminants to the web, which leads to unsightly errors on the finished printed product. Brand owners don't want to package their products in dirty and poorly printed boxes or labels, and printers don't want to be the ones to supply such packaging.
The appropriate static control and web cleaning product can work wonders for printers, reducing waste and protecting operators from harmful shocks. Both lead to increased profits and happy customers. Recently, packagePRINTING asked a few printers what units they use and why. This is what they said:
BISON BAG COMPANY, INC.
Bison Bag Company, located in Lockport, N.Y., prints, converts, and laminates a variety of films and other flexible packaging materials for many industries. Using flexography as well as the latest in digital technology, the company produces printed and plain poly bags and pouches.
Until recently, Bison Bag used static control bars with an eradication field of about 1˝. The bar helped eliminate some static charge, but not all of it and the result was bags that didn't stack well.
At CMM International in Chicago this past April, Jim Streicher Jr., company vice president of operations, stumbled across TAKK Industries Inc. After reviewing TAKK's anti-static equipment and receiving a generous offer, he chose the TAKK Ion-Edge AC Static Eliminator Bar and TAKK Ionstorm XR Static Elimination DC Pulse Bar system. He has been pleased with the equipment.
The TAKK bars offer a much wider field of eradication and a lot more flexibility in where the units can be placed on the machines, Streicher said. "With the older bars, the field of eradication was so small, especially on the wicketters where they only treated 1˝ on the top and bottom, and left the middle still staticy," he said. "With the TAKK bars, employees complained a lot less about the way the bags laid down. With the TAKK bars, we don't have to worry about the bar being so close to the web that it almost touches it."
The ease of use was another attribute of the TAKK bars that made Bison employees happy. "Basically, you plug them in and you can see the static dissipate and the bags start to lay flatter."
John Henry Co.
The John Henry Co. has been in business for more than 90 years. Headquartered in Lansing, Mich., the high-volume, narrow-web printer has eight facilities and has annual sales of more than $100 million.
Even with this success, the company was having a hard time dealing with the dust generated by paperboard stock. Since they supply packaging to the pharmaceutical industry and have to meet high standards, the company was scrapping as much as 20 percent of its printed product.
At the time, the John Henry Co. was using a web cleaning system with a rotary brush and many moving parts, which complicated the cleaning process and required the addition of tack rags to clean off the remaining dust.
While Eric Rosendall, packaging production manager at the John Henry Co., was leery of buying a new vacuum system to solve the dust problem, he changed his mind after trying a vacuum unit from Doyle Systems.
The day after the printer installed a Doyle system on its press, operators removed the tack rags and reported, "that if anyone took the Doyle web cleaner off the press, the operator would quit," he said.
According to Bob Jones, production leader of the Carton Packaging Department in Lansing, "It's an unbelievable difference. … Now they can run 40,000 to 50,000 pieces and not have to clean a plate because of the cleaner stock with the Doyle web cleaners."
A.S.P. Packaging Limited
A.S.P. Packaging Limited, located in Watford, England, converts flexible packaging films for fresh produce, hot bread, bakery, and prepared sandwich markets. Providing major United Kingdom supermarket suppliers with a range of the latest flexible products, it's important to keep production running smoothly and A.S.P. does so with Meech anti-static solutions.
Nothing short of the highest levels of customer service is acceptable to the demanding and fast-moving market that is A.S.P.'s customer base. A.S.P. meets these demands with static-free packaging. General Manager, Tod Hunter, explains, "During the converting process the packaging materials can accumulate considerable amounts of static charge which could potentially cause our customers problems when they come to use them. Therefore we remove that charge before our products leave our factory gates."
In addition to using Meech's conventional AC static products during the slitter-rewinder process, helping to reduce charge build-up on the material, A.S.P. has also installed Meech long-range Pulsed DC anti-static equipment on its high-speed wicketting machines, which run up to 400 cycles/minute. In this situation only long-range devices can be used and the Meech Pulsed DC solution increases the effective ionization range to provide an effective solution.
Left untreated, the static build up on these materials causes processing problems that result in more machine maintenance and downtime, as well as material waste. "A.S.P. has been using Meech static elimination equipment for many years to provide us with smooth production and packing processes," Hunter said. "The Meech solutions are technically advanced and very reliable, which to a company such as our own, producing in the region of 1,500 tons of packaging product each year, is absolutely essential."
TLF Graphics
TLF Graphics, located in Rochester, N.Y., has established a solid reputation for high-quality pressure-sensitive labels, labeling systems, and screen printed products over its 25 years. The company prints on a variety of substrates, including films, foils, papers, and adhesive and non-adhesive materials, using digital, flexography, hot stamp, screen, and offset printing.
Each job TLF Graphics produces has to meet its high standards. About three months ago, when the company realized its vacuum and brush web cleaning and static control system was no longer doing its job, Dave Manley, production manager, decided it was time for a change. "We were faced with the inability to get contaminate off the material," Manley said.
Manley, after evaluating several systems, went with a Julie Static Controls static bar with a MicroClean Technologies contact web cleaner. TLF Graphics immediately saw a difference. "On one particular job, we've seen a 25-30 percent decrease in waste," he said. "We see a lot more good product instead of the customer picking through it and rejecting it due to dust and other contaminates in the material."
TLF Graphics prints a wide array of jobs on its 4-color and 8-color presses, including high-quality work like wine labels. The new cleaning and static control system gave the company the ability to produce more of the work for which they are noted. "Overall, we saw a reduction in the amount of waste, across the board in all material we run because of this unit."
Tolas Health Care Packaging
Tolas Health Care Packaging has a lot riding on the cleanliness of its packaging jobs. The Feasterville, Pa.-company manufactures sterilizable packaging, including peelable or tear-open pouches and heat-seal coated lidding, for the medical device and pharmaceutical markets.
While excellent static control is required for clean operations and products, it's also essential to keep machine operators from being shocked—a persistent problem at Tolas. "Our operators were being zapped from the static electricity," said Ralph Eskilson, manufacturing engineer at Tolas. "Also, with sheet work, it builds up static charge and the sheets don't want to lay right."
Eskilson turned to SIMCO Industrial Static Control and the company's PerforMAX 3 Static Control system with a Blue Bar. Immediately, operators stopped getting shocked and sheet production got easier. Eskilson says the increased performance to the units' ability to emit ionization effects further from the bar, up to 15˝, he said. "It works well with the roll work we're doing," he added. "And we don't have blue flames coming off the machines giving operators jolts. We had static charges of 20 kV or greater. Now, it's gone down to practically nothing."
The PerforMAX unit also helps cut waste with the slitting required for Tolas' sheet work. "With static, sheets don't lay right and the sheets start to fly all over the place because of the charge, and that's not a good thing," Eskilson said.
In addition, with the pouches Tolas produces, stacking is a problem when static charges are present and the PerforMAX 3 eliminates the problem.
by Kate Sharon
Associate Editor





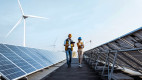