Addressing Finishing Bottlenecks in Package Printing
Demand for top-quality packaging in small, low-cost quantities delivered just-in-time is growing rapidly amid extremely competitive conditions. End users want innovative packaging solutions well suited to their customers' needs, tastes, and habits. To reduce time-to-market, end users are pushing tighter deadlines for the delivery of limited-run prototypes, customized packaging, and point of purchase (POP) displays.
For the folding carton converter, these trends dictate frequent, flexible responses, short runs, and fast job changes. Quality becomes even more important, since there simply is no time to react in the event of a production problem.
Continuous improvement
From prepress and workflow to efficient platemaking, the entire production process is being addressed on a continuous basis. Pressrooms boast ultra-efficient packaging presses capable of 18,000 sph running speeds and higher, along with a host of highly automated functions designed to banish bottlenecks, drive down makereadies, and increase productivity. In the converting departments, diecutters and folding carton gluers must continue to evolve to keep pace, while matching the highest quality requirements.
As in the pressroom, identifying and eliminating bottlenecks is a primary goal when it comes to maximizing the efficiency of post-press manufacturing. When you print faster, you have to be able to diecut faster, and so on, through folding and gluing. In both areas, the use of technology to streamline workflow, increase automation, and reduce handling saves time and cost—savings that then potentially can be passed along to grateful customers. Balancing capacity to ensure that jobs are pulled through the plant is critical in keeping work-in-process to a minimum.
Short-run diecutting
In response to trends like just-in-time delivery, and the proliferation of different SKUs, converters are running smaller quantities and changing tooling more frequently. High-volume producers equipped with highly automated equipment also are under pressure from their customers to handle shorter runs on a regular basis. Since lower volume jobs require more frequent tooling changes, converters and package printers are focused on achieving the quickest set-up times and reducing waste, rather than on absolute running speeds.
Long diecutting makereadies for short-run projects can be a waste of time, labor, and other resources. Reducing makeready times ultimately boils down to three things: a properly equipped machine; good tooling preparation; and superior organization.
Diecutter infeeds are designed for quick and easy setup. Both feeder head and feed table adjustments can be made in a few minutes. Some machines have sheet transfer systems that register the sheet and "place" it into the gripper bars. This sheet transfer is precise and greatly reduces trips to the feed table because of a misplaced sheet.
The chase—All modern diecutters are equipped with a centerline tooling system. At the cutting station, a chase changer unit permits the next die to be locked into the cutting chase while the machine is in production. A quick-lock clamping mechanism ensures that the position of the die is accurate and repeatable.
The chase changer unit is basically a rotating table that allows the cutting chase in the machine to be removed. When the table is rotated 180 degrees, the chase is ready for the new job to be inserted. This eliminates the need for heavy lifting.
Stripping—Moving to the stripping station, quick lock-up is again the name of the game. Quick lock-up frames for the upper and central tooling permit the speedy exchange of the upper and central tools. The most efficient setups keep the use of the lower pins to a minimum while ensuring reliable stripping of all waste; this requires the use of the so-called "dynamic" stripping system. Since dynamic stripping systems also require accurate alignment of the upper and central tooling, the machine can also be equipped with a micro-adjustment system to fine-tune the position for perfect results.
Blanking—The blanking station also should be equipped with a quick-lock upper frame, permitting the quick exchange of the upper and lower frames. Equipment is available that provides solutions for insertion of tie sheets into the blanked load for stability.
Good tooling preparation is essential to ensure that no problems are encountered when a job is set up and the machine is ready to run. This requires very close collaboration with the tooling manufacturer, whether an external specialist or an internal die shop creates the die. The die should be pre-nicked to about 90 percent of expected requirements. Rubber of the correct hardness must be used to minimize nicks and reduce marking. Finally, rubber should never be placed next to the rule, but positioned correctly away from it to ensure it does not pull the sheet apart. It is important to save the makeready sheet from the first time a job was run, as this will minimize patch-up when the job repeats.
Good organization around the machine is a must. Not only should the operator have fast, convenient access to the hand tools, patch-up tape, and other materials he or she needs, but all information about the job also must be brought to the machine, together with the pallets for the next job and the required tooling.
It is also important to inspect the tooling for any damage at the end of the run. Provided this is done systematically and any defects repaired, the tooling will be ready to run again when needed.
Process reliability at top speeds
To preserve the productivity gains realized in printing and diecutting, folding and gluing systems also must perform at maximum efficiency. Innovations in this area stem primarily from the use of automation to speed makeready through the use of computerized controls, and by combining and completing operations in one pass through the folder-gluer.
Automated changeovers promote short makeready times and greater consistency between operators. As an example, with Heidelberg's Diana folder-gluers, all lower carriers from pre-folder to the folding station are integrated into the AutoSet system for fully automatic makeready. Only a few blank parameters need to be entered for the machine settings to be calculated automatically. Machine control then relays the setting values to the digital position displays around the machine and the operator can activate the system. Since the machine moves the carriers in sequence from the feeder, rather than all at once, the operator can keep a close eye on the setup to ensure the carriers move smoothly into position. The operator also has the ability to make fine adjustments using the hand set, if necessary. The final machine position then can be re-stored into the memory for the next time the job is run.
More and more the folder-gluer is becoming a mini "assembly line" with multiple functions combined in a single pass through the machine. The open, modular design of most state-of-the-art folder-gluers permits the folding carton converter an almost unlimited range of customization options—collapsible box modules; turning modules; Kleen-Stik taping and tear-strip applications; windowing, insertion, inkjetting capabilities, and more.
Quality control
Integrated monitoring systems also have assumed a variety of time- and labor-intensive tasks that once fell to the machine operator. These include glue-line monitors, code readers, double-blank infeed detectors, window scanners, and equipment designed to eject any product that fails to conform to predetermined criteria. The removal of defective material ensures continuous production and consistent quality, enabling suppliers to deliver 100 percent defect-free batches without complex manual sorting.
As we have shown, folder-gluers have become extremely complex production machines that are not only capable of performing multiple operations, but can monitor each piece for quality assurance. Because the demands on the operator are high, good training and support are essential for best results.
The production of folding cartons in smaller quantities depends on user-friendly equipment capable of high processing quality, consistently short makeready times, and reliably high production speeds. Getting a job into production quickly and efficiently means removing as many obstacles to its timely completion as possible. Automated solutions have enabled folding carton converters to achieve significant performance improvements with a greater degree of confidence in the products they make.
About the author—Chris Raney is vice president, packaging for Heidelberg USA. pP
- Companies:
- Heidelberg





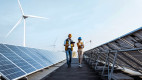