Combine and Conquer
Divide and conquer may be the key to success in some endeavors, but for package printers, combining processes is a clearer way to winning.
COMBINATION PRINTING MEANS different things to different people, but that's the nature of the beast. It includes different printing processes, along with various other processes, to accomplish one thing—add value to the printed product.
That is the game—adding value to the product to meet customer needs. By combining a number of processes, printers can use the strengths of each particular process to provide the best possible look for a product.
There are several requirements driving the popularity of combination printing, but they are all rooted in competition at the store shelf. Steve Leibin, sales manager for Matik North America (a distributor of Omet and Codimag printing presses), lists three interrelated needs that package printers are being required to meet: better print quality; improved shelf presence; and demand for products with the "no-label" look, reverse-printed, or with metallic/fluorescent labels.
Printers can achieve these results "by combining the unique characteristics of each printing process to offer labels with more visual impact," says Leibin. For example, screen printing can provide high hiding power and high color strength more effectively than flexo. With screen, converters can lay down a solid white on transparent self-adhesive materials. With gravure, Leibin says printers can print heavy metallic or fluorescent inks, varnishes, or thermo-sensitive inks for special effects. "The addition of screen, gravure, and hot-foil units are the most sought after combination printing units on the OMET Varyflex press," he states.
Ted Barry, executive VP for Matik, says the most popular combination press from Codimag (besides hot-foil stamping) has been screen with offset or letterpress. "Codimag and Stork have developed a semi-rotary screen unit that has been very successful," he says. "Many customers use the screen to put down a white pad on a clear label, then print offset over it."
According to Mac Rosenbaum, vice president, sales and marketing for Aquaflex, a branch of F.L. Smithe Machine Company, applications for combination printing are coming predominantly from the health and beauty segment. "It appears that the end-user [consumer products company] of the printed material is pushing the converters into this type of printing. The converters are being asked to be more and more creative in their graphic designs which, in turn, pushes their printing capabilities into combination printing."
For a package printer, having the ability to do combination printing can have a positive business impact. "At Aquaflex, we believe combination-printing systems create a printed product that has more value, which allows our users [printers] to gain market share and differentiate themselves from their competitors," says Rosenbaum.
Combining processes on one press involves both printing processes and other value-added processes that are really converting in nature, points out Ken Daming, director of product management, Mark Andy. As an example, he cites hot foil stamping which has been a value-added process for some time.
"What's new is the ability to add this process at any point in the press," says Daming. "For example, with some press designs like our LP3000, it's now possible to print, foil stamp, and then print again over the foil—all in one pass. The trend is certainly towards making presses more flexible in terms of the positions of the various processes. With our QC Cassettes, for example, it's possible to add flexo, screen, both hot and cold foil, diecutting, and now even ink jet at any point in the press—very easily and quickly."
In addition to this trend toward on-press positional flexibility, Gallus Product Manager Terry Trexler has seen a "highly renewed interest in hot foil stamping and rotary screen due to reduced tooling costs." Also, he sees more offset printing capability being brought into the value-added mix, mainly because of its known reputation for quality.
Gravure or digital in combo printing
The use of gravure and digital printing in combination applications is gaining popularity. Dick Chesnut, founder/owner/president of Chesnut Engineering, believes the use of gravure is one of the more significant trends in combination printing.
"Most press manufacturers are offering gravure capability in some way, either for coating or for printing in register with other units," says Chesnut. Although Chesnut Engineering has offered flexo/gravure presses for many years, about two years ago it began offering individual stations that can be hooked up with existing presses to expand their capability.
The interest in gravure goes beyond its a long-standing reputation for fine-dot process printing and good color control, says Chestnut. "Its significant advantage on combo presses is the ability to print very shiny metallics. While other print methods (flexo) do this to a fair degree, the results with gravure resemble hot stamping. The cost benefit by replacing hot stamping, however, is dramatic. This alone has provided the reason why both flexo printers and flexo press builders have now begun to use gravure."
In addition to its ability to print metallic inks, Daming points to two additional capabilities that gravure brings to the picture. It can provide a good solid opaque white lay down on a clear film or a lay down of heavy adhesives for cold seal applications in flexible packaging applications.
Gravure, though, is not the only alternative for opaque white and metallic inks, says Daming. "I do have to say, however, that I've seen rotary screen inks with a great opaque white and with metallic inks—and they are much easier and less expensive to run than gravure."
Leibin reports that Omet's new gravure cassette has become "very popular, very quickly. Rotogravure enables flexo printers to offer many special effects that can also be overprinted downstream."
He also points to an advantage he sees for gravure versus screen printing. "Downstream rotogravure printing units also offer higher production speeds than sceen printing units. This avoids compromising the high-speed production of UV flexo presses."
Digital printing in combination applications is a much more recent concept for package printing, and it bears watching in the near future. One of the issues for digital printing in general is its speed, and this comes to the forefront in combination uses also.
Rosenbaum states: "Digital printing stations for combination presses certainly offer some interesting capabilities. However, the performance of digital units has been somewhat slow in developing and their production speeds have not increased as the production speeds of the presses have during the past several years."
Mark Andy, for one, is offering digital printing capability and sees this as a big opportunity in the future. "We just introduced a single color ink jet station that can be mounted as one of our QC Cassettes," says Daming. "This allows adding the variable bar code or number in-line, in one pass without having to go to an off-line thermal transfer printing system. We believe there will be a huge demand for this combination process."
Whether it's state-of-the-art digital or more established hot stamping—or anywhere in between—the use of combination processes can provide a package printer with two critical elements for business success. It adds value to a printer's products and it can differentiate a printer from its competition.
By Tom Polishuk
Editor-In-Chief





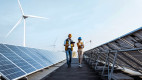