Best Practices: Adding or Upgrading Flexo Capabilities to Enter the Folding Carton Market

As brand owners seek new packaging applications to expand their businesses, it can have a substantial impact on what they need from their printers.
For example, if a brand previously only needed labels for its products but decides to implement a folding carton into its product line, a standard flexographic press may not be up to the challenge. In order to keep that business, a package printer may be faced with a decision to either upgrade an existing flexo press to handle these heavier substrates, or acquire new equipment altogether.
Increase Tension, Widen Idlers
The biggest difference in running label stock or film versus folding carton or another board style of substrate is the required tension. As substrates get thicker, the web tension will need to increase.
“When taking a standard press and upgrading to board, what you really need to be concerned about is the tension,” says John Baer, regional aftermarket sales manager for Mark Andy. “Board needs a lot more tension to run than just a standard label product. With this increase in pounds per linear inch, we may have to look at upgrading the tension controls throughout the press.”
The other major change that needs to be made to a flexo press so it can handle heavier stock is an increase in the diameter of the idlers. With thinner substrates, a thin idler is appropriate, as the application can be turned around an idler with a small diameter. However, as substrate thickness increases, a narrow idler can cause the substrate to rip or crack.
Baer explains that the idea here is to keep the board moving through the press as straight as possible, reducing the amount of bending it has to experience through the printing process.
“Larger diameter idlers will reduce the bend in the material,” Baer says. “You don’t want all these little bends going up and down throughout the press. You want to give it more of a straight plane from unwind to rewind.”
Effective tension management and larger diameter idlers can support heavier stocks on narrow web flexo presses.
When it comes to increasing the tension of a press, much of the focus is placed on the unwind. According to Tony Holmes, an application specialist for Montalvo Corp., which specializes in web tension, without the necessary tension, a printer running board could be met with an unwanted surprise as the end of a roll approaches.
“A lot of times with board, depending on the core size, when the roll gets down near the core, it tends to curl,” Holmes says. “The material can be tighter at the core and instead of coming off pretty flat like it does on the large roll, it tends to have the shape of the core. Often it is necessary to run higher tensions to get the curl out of the material.”
What’s Old Can Become New
While upgrading a flexo press designed for thinner stocks to take on folding cartons is possible, it’s not always the ideal solution. According to Justin Styers, president of Styers Equipment Co., which features upgrades and retrofits among its many services available to the printing industry, a standard flexo press will likely top out at 12 pt. board before the operator will run into trouble.
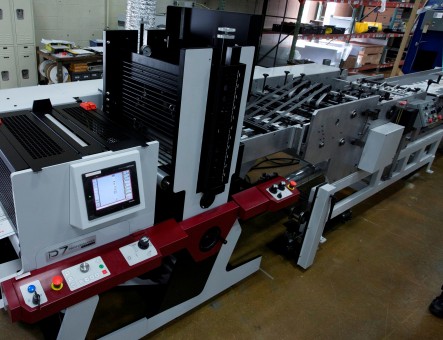
A robust die station and conveyor are important to address when adding carton and board to a press’s job mix.
“If you’re trying to turn a label press into a carton press, you’re going to run into a lot of issues with the impression cylinders, with the diameter of the idlers and your tension system,” Styers says. “You’re almost trying to put a square peg in a round hole.”
But instead of spending top dollar on a brand new press designed for folding cartons, Styers explains that there are several used options on the market. These used presses may not be immediately ready to join a modern production environment, but he says a company like Styers Equipment can make the necessary adjustments to an older press to bring it into the modern day.
Styers says some examples of presses that this can be done with include Comco ProGlide MSP presses and PCMC/Webtron presses including the 1600, 1618 and 1620 models.
“There are some great used options out there that are built for that particular process,” Styers says. “Those can be brought back to life by somebody rebuilding or retrofitting like we do.”
Bottom Line Decision Drivers
Before making a substantial alteration to an existing piece of equipment or introducing a new press into a production environment, it’s essential to determine how much new business this equipment will generate.
Baer explains that it’s important to understand that as a press gets upgraded to run heavier substrates, it means that it loses its capabilities to run the thinner materials it had in the past. Understanding the potential business and press time required by entering this new market should serve as the key decision point in upgrading a press versus buying a new one.
“Potential business would steer us toward upgrading what you have versus looking at something new,” Baer says. “In a lot of cases with minimal upgrade, they might be able to start dabbling into some thinner board materials and still be able to run the existing labels they have. It’s really dependent on the application.”

Cory Francer is an Analyst with NAPCO Research, where he leads the team’s coverage of the dynamic and growing packaging market. Cory also is the former editor-in-chief of Packaging Impressions and is still an active contributor to its print magazines, blogs, and events. With a decade of experience as a professional journalist and editor, Cory brings an eye for storytelling to his packaging research, providing compelling insight into the industry's most pressing business issues. He is an active participant in many of the industry's associations and has played an essential role in the development of the annual Digital Packaging Summit. Cory can be reached at cfrancer@napco.com