Executive Forum: Anilox Roll Engraving
Anilox rolls are often considered “the heart of the flexographic printing process,” as Dr. Lloyd Dreger of Laserlife points out below. As such, anilox rolls have played an integral part in the quality improvements that flexography has made in recent years in the packaging arena. To get a first-hand perspective on the impact these rolls will continue to have in package printing, packagePRINTING posed a series of questions to executives at the front lines of the industry.
pP: Flexographic printing has made great strides in improving its quality to better compete against offset and gravure. How have improvements in anilox roll technology contributed to this?
Aaron Lessing, director of sales and marketing, N.A., Apex North America—As quality demands approach and surpass those of gravure and offset, the anilox roll requirements have been directly affected. Higher linescreens of plates and higher speeds of presses both necessitate the following: LPI is increasing to produce finer plate screens; volumes have to be right on, as presses with significantly better tolerances leave less room for error; and consistent cell release has to be there, meaning that as the roll ages, surface tension or release characteristics must remain the same so that ink formulations don’t have to change due to a roll not releasing the same as it gets older.
Art Ehrenberg, vice president global manufacturing operations, Harper Corporation of America—Advances in release properties of anilox surfaces and new cell configurations have made it possible to continue increasing cell count and volume which aids tremendously in the ability to increase print fidelity.
David Skellie, president, Interflex Laser Engravers—Newer generation laser technology has allowed finer print quality through high-definition anilox line counts. These higher line counts also have increased cell volumes and enable printers to utilize finer plate screens that are necessary to compete with gravure/offset printing. High-definition anilox line counts allow the plate to print finer detail (1 percent dot on digital plates), yet bring up required densities.
Dr. Lloyd Dreger, technical director, Laserlife—The anilox roll, the heart of the flexographic printing process, is one of the major contributors to improving printing quality. The trend to more engraved cells per given area on the anilox roll surface has reduced the amount of air trapped in the ink. A cone of ink forms from each cell at the interface of the anilox roll and the plate cylinder. More ink cones for a given surface area means less air between cones. Less air in the ink results in a reduction of dot gain giving the printer the ability to print sharper edges on solids and lower percentage of process dots when doing process printing.
Additionally, the use of multi-hit circumferential engravings of ceramic-coated anilox rolls gives higher cell volumes and reduces doctor blade side shifting, resulting in better doctoring. Cell volume reduction due to wear of a ceramic-coated laser engraved anilox roll is not common, resulting in extended quality printing. Good daily cleaning and periodic laser cleaning of anilox rolls to remove the ink additives that build up on the engraved surface, such as poly-wax, silicone and Teflon, has shown to keep ceramic rolls producing top-quality printing for many years.
Dave Burgess, vice president sales and marketing, Pamarco Global Graphics—Anilox improvements have certainly contributed to the growing success of flexo. The keys to these improvements have been the precision of the latest generation of solid-state lasers and the systems available to measure and control the cell geometry and cell volume and, hence, deliver a consistent ink film thickness to the printing plate.
Pamarco has invested heavily in the new Thermal Yag Technology (ThermaFlo™ is our trade name for this type of engraving), which is solid-state, multi-hit technology. This process enables us to produce extremely smooth, consistent engravings with flatter cell bottoms, thinner walls to ensure better ink release from the cells. This process also allows us to cover a much wider range of volumes for a given screen count allowing printers to utilize the finer screen rolls for combination (solid and process) printing.
Mike McPherron, North American sales manager - printing, Praxair Surface Technologies—Innovations in laser engraving technology have unquestionably helped contribute to the advancement of flexographic printing. As recently as two to three years ago, the majority of flexible packaging printers were using 600 and 800 screen anilox engravings for their higher end graphics and process printing requirements. Today, many converters are now utilizing 1,000, 1,200, and even higher screen counts to improve their process printing and provide superior graphics. The rapid development and acceptance of digital plate processing technology has fueled the drive for higher screen counts and top quality graphics.
Recent enhancements in laser technology and software advancements have provided new and innovative engraving patterns, deeper cell depths, and greater ink carrying capacity at these higher screens for anilox engravings.
David Lanska, Canadian regional sales manager, Stork Cellramic—There is no question that flexo quality has improved as a result of improvements in each of the major press components. The catalyst driving those improvements is the quantum leap in anilox roll technology brought about when laser energy was applied to the task of engraving into plasma-coated ceramic. The engraving that resulted was much more versatile and durable than anything in the market. Its ability to carry more ink at finer line counts enabled printers to achieve color at higher levels of quality than were ever imagined.
pP: Laser technology has made its mark in anilox roll engraving. Does mechanical engraving of anilox rolls offer any significant advantages?
Lanska—Mechanical engraving continues to have a niche because of the price advantage it has over ceramic laser-engraved rolls. The lower initial price is attractive, especially for applications that do not require a high level of print quality, (particularly for those jobs still run roll-to-roll). When run against rubber nip rolls, mechanical engravings can last for several months or even years, making them a good value.
Mechanical engravings are also suited for situations that are predisposed to a high rate of roll damage. In this case, the expectation is that the rolls will become damaged long before they would wear out, so there is little justification for the added cost of laser-engraved anilox rolls.
While mechanical engravings may have a lower initial cost, the cost advantage quickly dissolves once the rolls are run against a doctor blade. In bladed applications, the laser-engraved ceramic roll tends to outlast the mechanical engraving by two to five times or more. The added durability yields a lower total cost of ownership. Combined with the vast improvements in print quality and consistency, as well as reduced makeready costs, the laser-engraved ceramic is by far the superior value. Lessing—Mechanical anilox rolls have, for the most part in flexographic printing, fallen behind laser rolls; we estimate that they account for 5 percent or less in the North American marketplace. This is due to a laser roll’s superiority in print capability (finer linescreens, better density); life expectancy (a laser roll will outlast a chrome roll at least 5:1 if well maintained); and price (a laser roll 10 years ago was five times the price of a chrome roll, now in many cases, and depending on the supplier, it can be as low as twice or even less).
Ehrenberg—Chrome-plated, mechanically engraved rolls can have significant life in roll-to-roll metering, and when dealing with very heavy film thicknesses of high-viscosity materials, mechanically engraved chrome continues to be a good choice due to its release characteristics. However, wear will continue to plague any wide usage of this product. As laser engraving of ceramics continues to evolve, I believe the life cycle of chrome-plated mechanical engravings will eventually come to an end. Environmental issues as well continue to drive the plating market down.
Skellie—Unit cost could be considered an advantage, however, users must consider the costs incurred for re-chroming of mechanical engraved rolls. Consider the gains being made in laser technology with regards to engraved cell performance along with the lifespan of the ceramic anilox rolls verse the limitations of mechanical engravings along with the environmental issues surrounding heavy metals.
Dreger—Mechanical-engraved anilox rolls are limited to about 500 cells per inch. Close packed 1,500 cells per inch are now common for ceramic-coated laser-engraved anilox rolls which are used for high screen process printing. Originally laser-engraved ceramic anilox rolls were five times more expensive than mechanically engraved rolls and could only be justified on a much-improved lifetime of such rolls, or where improved printing quality was needed. The price of laser-engraved ceramic rolls has come down considerably. When roll wear, wet-ability, dot gain, and corrosion are not problems, mechanical-engraved rolls can still compete. Unfortunately, environmental and regulations for hexavalent chromium emissions (cancer causing) during chrome plating have increased the cost of mechanical-engraved rolls.
Burgess—Pamarco Global Graphics still has a very strong mechanical engraving business but this is mostly now in the field of coating and laminating. These processes typically require volumes greater than can be achieved currently by laser engraving (in excess of 50 BCM) or require channeled cell structures due to rheology of the coating material being used. There are now very few mechanically engraved, chrome-plated rolls being used in the typical flexible packaging market due to the rapid wear experienced by the chambered doctor blade systems.
McPherron—There are still a few market segments that require mechanical engravings. This ink metering technology is limited to rubber metering rolls (rather than doctor blades) and the prospect of achieving reproducible high-quality graphics over long print runs is very limited.
Tougher environmental considerations, in particular stricter plating regulations, will further hinder the growth of mechanically engraved, chrome and copper plated anilox rolls. We predict the continued decline of mechanically engraved rolls.
pP: What market trends do you see that could impact your business for better or worse over the next five years?
Lanska—A major push is underway to reduce makeready times. More and more printers are realizing the tremendous drain that extended makereadies have on raw material consumption, waste generation, and profitability. We expect that to translate into better attention to proper roll maintenance, standardized roll specifications, and improved anilox inventory management.
Lessing—For Apex Group, we are extremely optimistic over the next five years. As the marketplace becomes more integrated and global, it becomes all the more important to be global yourself. With our two full-service manufacturing locations in Europe and North America, and soon to be in Asia by this summer, we can offer sales and service on a high and equal level around the globe.
Pete Hartman, VP sales, Harper Corp. of America—The continued demand for high-end graphics on the retail shelf will continue to create a demand for high-end aniloxes to produce the best print possible at the lowest cost and at the highest speeds. The continued push for lower pricing will continue to challenge all suppliers to be as efficient as possible to keep their own cost in line as well.
Skellie—The demand for an anilox roll that suits both solid and fine process work has been a niche market for the high-definition anilox. This high-definition anilox technology also allows for less roll inventory and reduces changeout time for the press.
A negative impact that our business is feeling now and will feel for years to come is the constant “beat down” of anilox roll engraving price. With quality comes the cost to maintain the highest level of service and technology.
Burgess—The move to gearless presses in the short-to-mid term is having a very positive effect on the anilox business. A converter buying this type of equipment for the first time may purchase as many as 30 to 40 new anilox sleeves for a 10-color press because he now has the quick change ability he needs to print an enormous variety of short-run work.
pP: What technology developments are in the works that could provide further improvements to the performance of anilox roll engraving and/or anilox roll performance?
Burgess—Pamarco is focusing its resources on the ceramic coating and laser-engraving technology. The chrome oxide ceramic coating is a key ingredient in the development of the anilox roll particularly as we push the screen counts higher and higher. The ceramic must be a very hard, dense, homogeneous layer with a minimum level of porosity, yet still be engravable. Pamarco has installed a unique coating system into the U.S., which actually will produce a coating that produces hardnesses in excess of 1,400 Vickers (1,150 and above is the industry-stated standard) with density and porosity readings well below the industry standard 2 percent level.
Lanska—New engraving technologies are poised to increase engraving efficiency and expand engraving capabilities. It is important to keep in mind, however, that each time we have introduced the industry to a new engraving technology, (whether CO2, YAG, multi-hit, and most recently, fiber optic) the development curve has taken considerable time, effort, and money. There were bumps along the way. Once these technologies were developed and refined, they provided significant improvements in cell geometry, which translated into improvements in print quality.
It is never a good idea to rush a development. Current engraving technologies are capable of producing engravings over 2,000 LPI. Since most print shops top out at about 1,000 LPI, the industry as a whole has a long way to go to catch up. Anilox inspection and cleaning methodologies need to continue to evolve.
Lessing—Third generation anilox sleeve development is the hot topic here: less weight, less cost, better tolerances, better construction. A fiber composite concept design will cut weight by a factor of five to 10 times, and will maintain its tolerances throughout its life. Conventional anilox sleeve weight is up to 1 lb. per inch and they have a life span of two to four reworks. This new sleeve construction will only have a lifetime of one engraving, as it is designed to be a “throwaway.” This factors in well when you consider that the cost of this new anilox sleeve complete will approach the cost of a typical rework on a conventional anilox sleeve. In other words, inventory costs can be reduced to the cost of a rework, a printer is no longer carrying the cost of a $1,200 to $1,800 sleeve, plus he/she doesn’t send it out for rework—they simply reorder new.
Skellie—Fiber Optic lasers with multi-hit and modulated beam technology. This technology produces a smoother, consistent cell with improved ink and coating release characteristics.
Dreger—The biggest problem with high-surface-tension, laser-engraved ceramic anilox rolls is that they lose their high surface energy over time. This is due to additives like poly-waxes silicones, and Teflontm particles that are in the inks attaching themselves to the engraved surface. The low surface tension (non-wetting) of theses materials comes across as lower ink volume delivery. Thus, many customers feel their rolls are wearing out too rapidly. Due to the chemical resistances and malleability of these materials, chemicals soaking and grit blasting doesn’t work. The only way to really get rid of the film is with laser cleaning of the roll—literally vaporizing off the poly-wax, silicones, and Teflon. ... Work is being done to improve the surface finish of the engraving to reduce the attachment of these small particles of ink pigments, poly-waxes, silicones, and Teflon to the cell walls.
pP: Is overseas competition impacting your business in any significant manner? If so, how can this be combatted?
Dreger—No! The ceramic-coated, laser-engraved anilox roll technology, which is the majority of our business, was developed here in the USA, and with time and money spent to improve the process and thus the quality of the printing, we will continue to be the best.
Burgess—Overseas competition is having some impact, particularly with new press installations as most of them are built outside of the USA. The long-term fear is certainly that anilox sleeves could be shipped from across the Pacific at a lower cost, but we firmly believe that most high-quality converters are looking for a local level of service, expertise, and rapid response that will make overseas supply difficult.
McPherron—Praxair is unique among anilox engraving suppliers in that we have seven global manufacturing sites strategically placed to serve the major printing markets. This global manufacturing and service strategy allows Praxair Surface Technologies the opportunity to provide optimized regional manufacturing and distribution while offering local customer sales support and superior technical service.
Lessing—Overseas competition is not affecting our business in a negative way; if anything, it is helping us: Apex Group has built very strong relationships with OEMs around the world, so many times, when a machine enters the North American market, we have our anilox rolls/sleeves already installed on the machine—a nice door opener, as you could imagine. In fact, it is due to this that Apex North America opened its doors here in the first place. With all of the good suppliers already in the U.S., it would have been unreasonable to assume that a converter would send his business back to Europe or Asia. So we simply decided, “If you can’t beat ‘em, why not join ‘em.” We have not looked back since.
Hartman—Overseas competition is showing up more and more in the marketplace. We need to continue to offer a well-rounded value package that satisfies all of the customers needs. Also, we must continue to produce better quality in a more efficient manufacturing environment.
Skellie—Not currently, however with more sleeve presses coming into production and prices for engraving continually being driven down overseas this could become a factor in the future with regards to the lower cost of shipping. n
- Companies:
- Pamarco Global Graphics

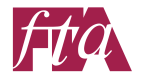
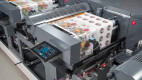

