Muscling Forward
"A job-shop on steroids"—that's Bema Incorporated President Glen Galloway's catch-phrase for the 51-year-old, Elmhurst, Ill.-based film printing/converting firm he has owned since 1999. When Galloway took Bema's helm, he set out to bring this catch-phrase to fruition by elevating the firm's long-time job-shop operations philosophy, instituted by founder Sam Shaw, to a super-sized level of implementation. His plan to achieve was characterized by a more targeted focus on continual customer service improvement and, most recently, four consecutive years of significant technology and infrastructure investments.
Under Galloway's leadership, Bema has cultivated a strong vertical integration of its operations—which now include a digital prepress technology center, plus 10-color flexographic printing, adhesive lamination, slitting, bag-making, and pouch-making capabilities—all housed at its Elmhurst facility. Galloway believes this capabilities structure is a notable competitive differentiator for the smaller, 48-employee firm, and Bema's customer base would appear to agree; Bema's small-company operations philosophy and large-company capabilities blueprint has proved a powerful combination, helping the firm triple sales in the past four years and cement a presence in the food, pet, and industrial markets.
This strategic approach also enables Bema to consistently meet complex, custom film production requirements. A typical day on the production floor could include printing, laminating, and/or converting a host of film substrates, including polyethylene, polyethylene terephthalate (PET), polyvinylidene chloride (PVDC)-PET, biaxially-oriented polypropylene (BOPP), and nylon, as well as a number of specialty films. A typical printing or converting job could require adherence to the American Institute of Baking (AIB) Superior Certification or other strict food safety and quality certifications—a common requirement for Bema's nut, meat, and tortilla packaging customers. It could also require the accommodation of a variety of final converted product requirements—such as the one-stop-shopping capability to deliver roll-stock, bags, and/or pouches (a frequent specification for Bema's pour customers).
"We can respond, react, and change faster than the companies that we serve, and the larger companies that we compete against," Galloway sums up, citing Bema's ability to typically turn jobs around in half the industry's standard lead-time of four to six weeks. The key to this competitive advantage, he notes, is to pursue equipment investments for the purpose of added flexibility, rather than to simply bolster capacity.
Toning up makeready
Bema's latest initiative to fortify its über job-shop reputation is the purchase of a new Windmoeller & Hoelscher (W&H) 52˝ 8-color MIRAFLEX AM flexographic press—technology debuted by W&H in late 2009. W&H designed the MIRAFLEX line to more economically answer the needs of firms that produce small- to mid-sized print jobs on a daily basis.
According to Galloway, the primary benefit of the MIRAFLEX press for Bema will be faster makeready. "As we continue to become familiar with this new press technology, we anticipate that our makeready times will go down, running speeds will go up, quality will improve, and most importantly, our customers will be more satisfied," he elaborates.
To this end, key quick-setup features of the MIRAFLEX include its EASY-SET automatic impression setting, EASY-REG registration, EASY-COL color matching system, and TURBOCLEAN automatic ink supply and wash-up system, which enables ink changes on all decks in under five minutes. The line will be capable of printing speeds up to 1,200 ft./min.
The MIRAFLEX investment marks Bema's second installation of Windmoeller & Hoelscher press technology in the past four years. Bema purchased a 10-color PRIMAFLEX from W&H in 2007, which has been processing all of the firm's print jobs and will remain an integral part of its print production line.
Explains Galloway, "Actually, you not only make a decision on the type of equipment you want to buy, even more important, you make a decision on what company you want to support the equipment you buy." He further notes that Bema has found "a manufacturer that builds a great product and provides exemplary service" in W&H, and "that is why we are installing our second W&H press."
Well-defined pouch operations
Pouches are one film application area with strong potential to frequently grace Bema's new MIRAFLEX line. The press's quick-change features will play a pivotal role in the company's ability to manage the demand for shorter print runs and "faster-to-market" lead times Galloway is seeing in the pouch market, as well as in many other aspects of Bema's flexible packaging business. He believes these demands primarily stem from the expansion of the private label market, and projects that the increasing interest in smaller runs of higher-end private label flexible packaging will feed substantial growth in the pouch market.
General growth in demand for pouch printing and converting has already been a driver behind several other recent converting and finishing equipment investments at the firm. While Bema originally outsourced a portion of its pouch business, the firm brought pouch manufacturing completely in-house more than two years ago in response to customers' requests for reduced lead times and costs. Galloway adds, "In keeping with our vertically integrated manufacturing philosophy, entering into the pouch manufacturing market was a natural transition for Bema."
The firm rolled out in-house pouch manufacturing capabilities in October 2009 with the purchase of a pouch machine from Karlville Development Group. Increased volume prompted the installation of a second Karlville machine in July 2010. Like the MIRAFLEX, these investments support Galloway's ultra job-shop vision for the firm by providing the flexibility to produce a variety of pouch types, including stand-up designs in a variety of sizes, as well as side-gusseted and pillow-pack designs. Further, these investments in flexibility position Bema favorably to manage customers' heightened attention to flexible packaging sustainability. This is a trend that Galloway believes will not only affect the range of substrates used in pouches, but also the specifics of the pouch manufacturing process.
Long-term strength in flexibility
While Bema's extreme job-shop culture gained critical long-term heft with the purchase of the Windmoeller & Hoelscher MIRAFLEX, Galloway maintains that the firm's ongoing commitment to investments in equipment for flexibility will remain strong across the full breadth of its operations. For instance, in its digital prepress department, where a recent installation of a DuPont Fast System has already helped reduce lead times and improve print quality, Bema is now introducing HD flexo plate technologies that cost-effectively enhance these benefits. In addition, Bema's expectations for continued growth in pouch manufacturing volume have given rise to plans for a third Karlville Development Group pouch machine installation toward the end of 2011.
Still other pending investments could mark a significant infusion of both flexibility and capacity for Bema; the firm is currently finalizing plans for a second Chicago-area facility that Galloway says will initially host warehousing overflow, but later accommodate expanded manufacturing capabilities. In another five to seven years, Galloway expects his "job-shop on steroids" to stretch its capabilities in yet another new direction—with an expansion to a western U.S. location. pP

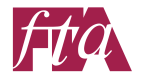
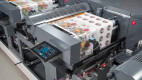

