Anilox Engraving
Flexographic printing’s gains in the market are unmistakable, and the quality of its end products continues to improve. Anilox rolls are a key component in the quality equation in flexo printing, and also in the equation for its productivity. Improving prepress operations for flexographic printing means, in part, improving efficiencies of anilox roll change-out and preparation. To a large degree, anilox roll preparation equates to engraving.
Anilox sleeves are enjoying increased usage in this arena, and some might be surprised that the sleeved alternative to engraved anilox rolls can sometimes exceed the LPI (lines per inch) of rolls. Plus anilox engravers can employ the same cutting-edge processes, such as laser engraving, on sleeves as they can with rolls. There are pluses and minuses to using rolls and sleeves or vice versa, many of which deal with volumes rather than the actual applications.
Engraving rolls and sleeves
Despite the type of anilox device you spec, the full gamut of engraving techniques is available, including laser engraving. The engraved surfaces, in general, are the same. “Most anilox sleeves have an outermost layer composed of metal, typically aluminum,” says David Lanska, midwest regional sales manager, Stork Cellramics. “This surface reacts to processing in a very similar fashion to a conventional steel core. Once overcoated with ceramic, the laser reacts the same to the sleeve or the roll.” He adds that once the sleeves are mounted on air cylinders, the processing steps are nearly identical for sleeves and conventional rolls.
According to Dave Burgess, vice president, sales and marketing, Pamarco Global Graphics, there are no differences in terms of engraving between sleeves and rolls. “They are both prepared for laser engraving by applying a heavy layer of chrome oxide ceramic, diamond grinding, and then diamond polishing,” he says.
Of note is sleeves’ sensitivity to temperature. Lanska states that the internal construction of the sleeves means temperature control is critical during the plasma coating operation, “to prevent degradation of the composite and compressible layers.” He also adds, “The materials typically used for sleeve construction do not stand up well to heat or caustic chemicals. Repeated exposure to these can cause the layers to break down and lead to catastrophic failure of the sleeve.”
Lloyd Dreger, technical director, Laserlife, adds that one must be careful in coating sleeves with ceramic because the thin aluminum layer is not sufficient to conduct away the heat generated in the process. “You also have plastic present, which cannot tolerate high temperature without deterioration,” he says.
Print quality
Both anilox rolls and anilox sleeves have comparable print quality. In practice, it depends on the print job. Some anilox roll users use rolls with lower LPIs than their sleeve counterparts, but this results from compromises in screen and volume combinations. “There are many non-sleeved presses that use high screens, but generally the screen range will be more limited as it takes the converter longer to change out rolls,” says Burgess. “So they develop compromises with their screen and volume combinations.”
Alexander James, technical graphics manager, Harper GraphicSolutions, says, “Sleeves are generally used for wide web, and print at higher speeds. As a result, the cell per inch engravings compared to narrow web [rolls] are on average not as high.”
However, according to Lanska, the use of servo technology allows for sleeve LPIs to be on the high end of the scale. “Like conventional anilox rolls, anilox sleeves can be engraved to the entire gamut of engraving specifications,” he says. “Generally, however, anilox sleeves are suited to high-end process printing because of the precise ink placement and registration control afforded by servo technology. For that reason, they tend to be on the high end of the LPI scale.”
Burgess adds, “The reality is that the majority of sleeved presses are producing high-end products at relatively high speeds utilizing chambered doctor blade technology. The engravings for the typical sleeve presses will vary in range from standard 250 screen up to and above 1,000 line screens with higher than standard volumes.”
Aaron Lessing, director of sales and marketing, North America for Apex North America, comments that the only difference is “with gearless presses, where sleeves are prevalent, because of the sophistication of the technology. Converters can run higher quality jobs if they choose to, and therefore run finer anilox engravings.”
Pluses and minuses
Rolls and sleeves both have their places in flexographic printing, and there are advantages and disadvantages to each. Sleeves, on the whole, remain more expensive and have storage issues. With rolls, the larger the roll, the longer the makeready. Dreger states that the big advantage in using sleeves is that roll changing time is cut from hours to minutes, so downtime is a lot shorter. Conversely, rolls are steadier and a more stable system for delivering inks, but the changeover time can be long.
According to Burgess, the current limitation of traditional sleeve length is currently about 83 inches, “which is a limitation, although as the sleeve gets longer, it does get heavier and harder to handle, so going over this length may be defeating the purpose of ease of handling and quick change,” he says. He adds that their ease of handling can be an obstacle. “The biggest issue that we see with sleeves is that they are too easy to handle and therefore susceptible to simple handling damage, being stored on their ends, and fracturing the ceramic,” he says. Additionally, a typical anilox roll that has been frequently reworked could suffer from an out-of-balance condition if any weights have come loose or rolls have been bent and straightened leading to thin and thick walls.
James cites maintenance, handling, and care as the most significant issues for sleeves. “It is very easy to damage the ends of the sleeves when removing and reloading them onto the press,” he says. “Storage for sleeves should be vertical or supported with a wide tubing when stored horizontally.” Cleaning practices for sleeves, he says, should have explicit directions that follow manufacturers’ recommendations regardless of what type of cleaning system is being used. “Additionally, care must be taken when loading and unloading of sleeves from the press mandrel,” he says. “The sleeve must slide smoothly in either direction. If the sleeve binds up and the operator waddles the sleeve around the mandrel, the inner construction of the sleeve can be damaged.”
“A big problem with sleeves of standard construction is there is foam, glue, and the type of aluminum being used, as well as end caps falling out,” says Lessing. “The end result is sleeves with shelf lives of two to four reworks before delamination of the foam or TIR (total indicated runout) [takes] place, or the end caps fall out. This can be irreparable.”
Lanska asserts that conventional rolls hold an advantage in durability. “When properly cared for,” he says, “and journals [are] repaired as needed, they can last indefinitely.” With sleeves, he adds, the inner winding and compressible layers can break down over time, especially when exposed to high pH cleaning chemicals or the heat of the plasma coating process. “Failure of the sleeve construction requires replacement, whereas conventional rolls can be repaired or built back up through welding or thermal spray coating,” he says.
Burgess concurs. “The standard, integral-shafted anilox roll is still a very common and viable product in the marketplace,” he says. “If built correctly to specifications, the roll can be reworked many, many times and exacting tolerances can be held.” However, he adds that a typical anilox roll coming in for refurbishment usually requires extensive bearing journal repair work and re-centering of the roll to make sure that the roll will be within the manufacturer’s stated dimensional tolerances.
Rolls, however, can be very heavy. Each roll requires its own set of gears and bearings. “On some presses, the extra tooling can be very expensive,” says Lanska. “Because of their integrated journals, rolls take up more space in storage.” He adds that the weight of conventional rolls requires material handling equipment and much sturdier storage racks.
Cost is another advantage of rolls. According to Lanska, the unique construction of the sleeve is a time-consuming and expensive process. As a result, sleeves tend to cost two to five times as much as conventional steel anilox cores.
“The ergonomic benefits of sleeves versus integral anilox rolls are well documented, [including] ease of handling, speed of changeover, interchagneability from one engraving to another, and easier storage,” says Steve Wilkinson, general manager, ARC International. “The downside of sleeves is the relatively short time frame that a sleeve can lose its engineered tolerances during normal running, as the internal expandable structure hardens and softens due to the heat buildup, work hardening, impression set, and mechanical damage that can and does occur in varying degrees dependent on the time that the sleeve is run.” pP
Foamless sleeve construction
Apex Ultraquick™ Sleeve technology and the conventional sleeve eliminates the flexible foam layer and the glue that holds it in place, replacing it with Apex’s patented aluminum rings. Foam has memory issues. As it is loaded and unloaded from the air mandrel, and compressed and decompressed, it “forgets” where to go over time and can delaminate. This leads to either the sleeve “sticking” to the mandrel, or “slipping” when the mandrel is put into drive. This typically can happen about two to three years into the life of the sleeve. Either of these conditions is unacceptable.
According to Apex, other benefits of Ultraquick sleeve technology include:
• All layers are extremely stable, the sleeve will not go oblong over time.
• Very high integrity of the construction. Nothing moves except for the inner sleeve expanding and contracting via the aluminum rings.
• Inner sleeve is secured within sleeve construction.
• Outer aluminum is cast for stability. It does not move during manufacturing or in the printing press and is lightweight. Conversely, seamless aluminum tends to go oblong over time.
• TIR starts at 0.0002˝ to 0.0003˝ and is maintained throughout its life.
• A metal end ring protects the inner sleeve and is mechanically fastened. Glued end rings tend to fall off over time.
• Resistant to contact with mandrel for repeated changes. The inner sleeve is made of a very stable composite material and does not fray over time, which can cause vibration.
• Protects edges of ceramic with bevel. This will reduce the chances of chips in the end of the sleeve, which could tear up doctor blades.
• This sleeve is dynamically balanced for high speeds.
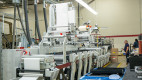




